I’ve just finished weaving my way through the lively, narrow streets of Tokyo’s Harajuku district, roller suitcase in one hand, umbrella in the other, tired and soaking wet in the warm summer rain. And yet I couldn’t be happier. After a 3-hour trip north from Osaka I’m on the doorstep, literally, of one of the most praised and sought-after denim brands in the world: Pure Blue Japan. Invisible from the street, the only hint to what lies inside is a small, distressed metal plate depicting an indigo leaf, affixed to the streetside wall.
They’re expecting me, but still I hesitate for a moment outside of the shop, as much to gather my courage as to catch my breath, and take a small break from all the walking. I’m finally here. All is good in the world. So with that, I close my umbrella, grab my needless suitcase (why did I bring this damn thing?), and head up to meet the master himself, Kenichi Iwaya.
I’m greeted at the door by two lovely (and very knowledgeable, it turns out) female employees, both of whom I had mistakenly assumed to be men during our pre-interview emails. The shop itself is quite small and minimalist, but very tastefully done in beautiful wood shelves and fixtures, as they giggle at my Osakan accent and I giggle back at the fact that they are giggling at my Osakan accent. Small talk taken care of, soaked suitcase now suitably stowed, I am taken up a very steep flight of stairs to the workshop above the store where Iwaya-san is waiting for me.
Have you ever met those kind of people where, when you talk to them, everything just seems like it’s going to be alright? Like they already know what happens at the end of the game, so they can just be happy and content while the rest of us scramble around trying to figure out the right thing to do? Iwaya-san struck me as that kind of person, somebody who is truly satisfied in their chosen walk of life and exudes a certain kind of confidence and calmness. Yes, if my plane ever does make an emergency landing on water (does that ever really happen?) I want Iwaya-san to be the guy calmly unbolting the door and throwing it as far from the aircraft as possible. But I digress… This is not my story. This is the story of a man and his dream to make the best denim and jeans possible. So here it is. I hope you enjoy it.
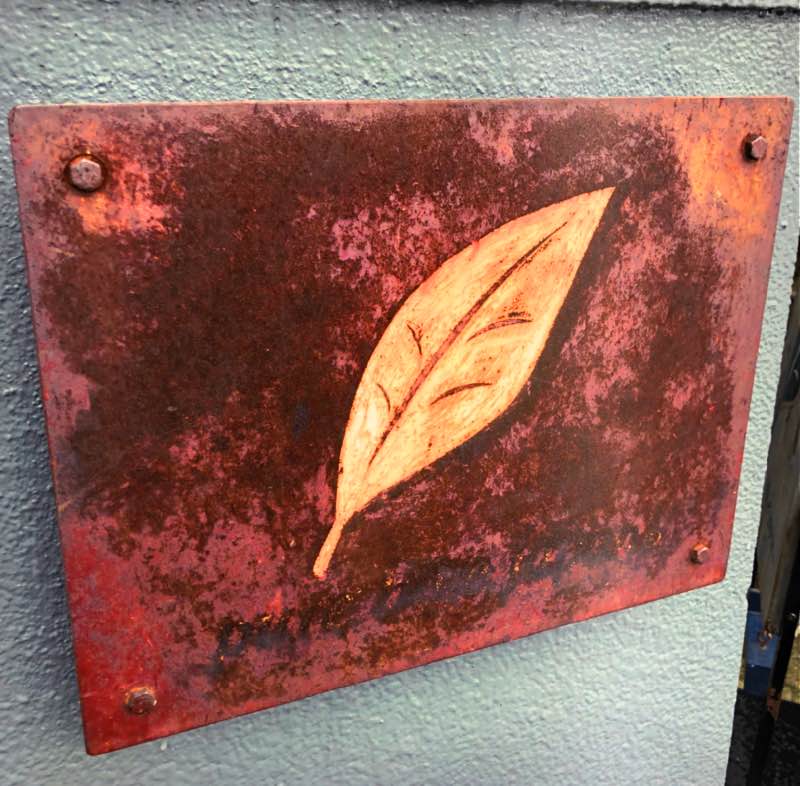
Thank you so much for making time to chat today, I really appreciate it.
Not at all, no problem. Thank you for coming all this way.
So maybe we’ll start back even before Pure Blue Japan. What were you doing before you made jeans?
Well, I created Pure Blue Japan in 1997, but for about 7 years before that I worked for a company in Okayama that sold fabric to different makers, so I was able to form good relationships with the mills through that job. At that time you had makers like Evisu, Full Count, and Warehouse…you know, that was like the heyday for denim here, so for me, I started to think that making jeans would be more interesting than selling fabric, so I thought I’d give it a try.
Wow, just like that. So, you’re from Okayama then originally?
No, I was actually born in Osaka, but we moved there when I was young because my dad got transferred there for work.
And you still live there?
Yes, I’m still in Okayama.
So fast-forward to you wanting to actually establish your own company – what made you decide to do that? What was driving you at that time?
Well, I wanted to make jeans myself, but I had never done it before. I actually thought that out of all the different types of clothing you could make, jeans would be the easiest because there aren’t that many parts to them but…I really had no idea because I’d never done it. (laughs) But I just went ahead and did it and, as you can guess, produced some pretty awful stuff at the beginning. But even by 1997 we didn’t have the internet you see so…
Ah true, I never thought of that.
Even though I lived in Okayama, I came to Tokyo to start my business, the reason being that there would have been no way to get any information out at that time living in the Okayama countryside. I thought coming to Tokyo would be only way to do it, so I came here and started selling, but I didn’t have my own store and I didn’t really know anybody here who did have their own store so…things were mostly sold through magazines at that time and that’s the way I started out too.
Magazines? Wow, how times have changed. Were there any other kind of challenges or setbacks you faced back at the start?
Well, there was of course the fact that I’d never made jeans before (laughs), but because I had worked at a fabric company in the past, working with makers and delivering between them and the factories, getting to know them, I think I at least had a pretty smooth start in that regard.
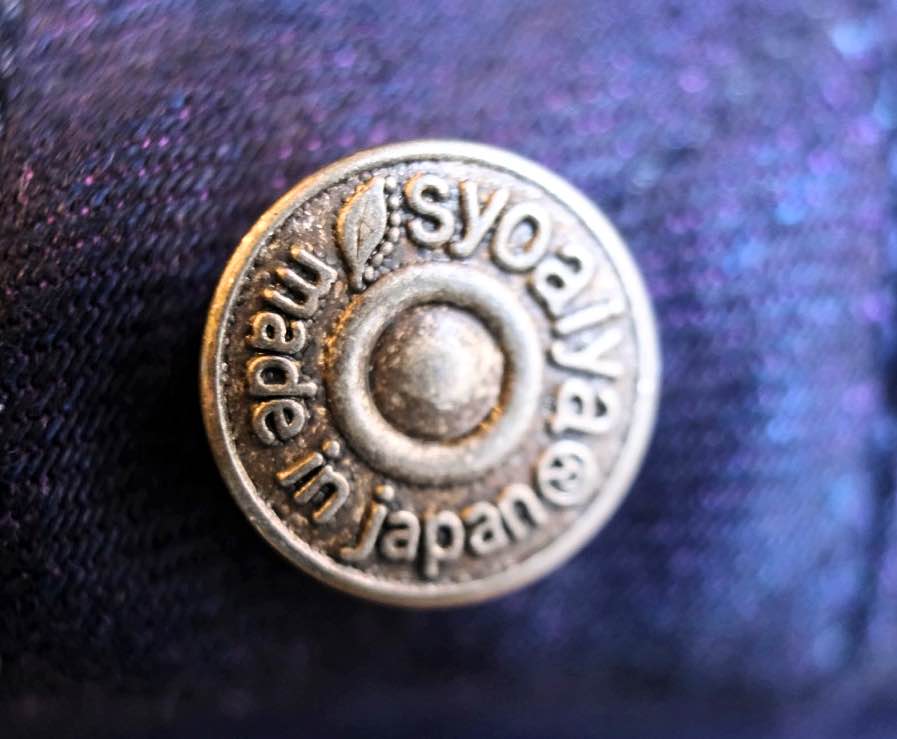
Did you have like a mentor or somebody to teach you or help you at all?
Not at all.
Just yourself.
Just myself. And my dad was just a regular salaryman so…
I see. And were you satisfied at all with what you were able to make at first?
Not at all. I would look at the jeans I made and then look at something from Warehouse or Full Count and it was obvious that they were completely different from mine. But because I’d never done it before, I couldn’t even tell what it was that was different. (laughs) You could tell immediately that those guys were on a different level but…what the heck was I doing wrong?
Looking back, what was it that was different?
It was the shape. The fabrics themselves weren’t really that different from each other back then so, yeah, it was the cut, the shape.
Do you still have any of those early attempts?
No, they’re long gone.
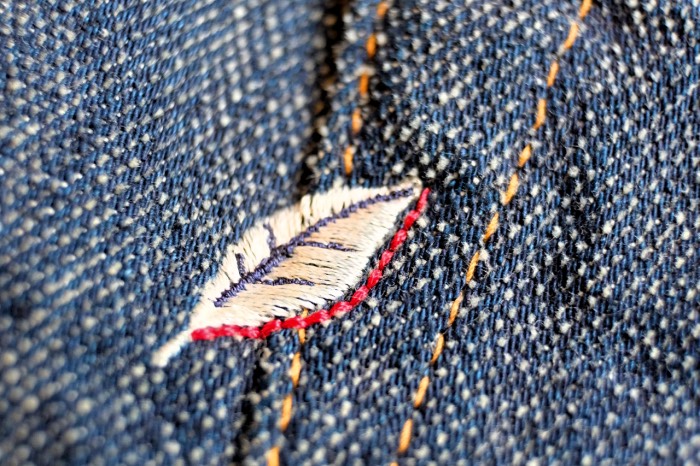
Okay (laughs). So how about new ideas, patterns, fabrics and such?
Well times have changed since the beginning, but it would have been nice if we had selvedge back at the very beginning. Japanese jeans really started with selvedge and vintage replicas, and more and more brands starting making jeans in their own way, each eventually starting to say like, “I want to use this kind of fabric, my jeans need to be sewn in this way, this way won’t do, etc”. But these techniques that we makers all thought were difficult or special back at the start have sort of become standard among us now – everyone can do them. The technical part is now taken for granted, it’s kind of obvious. So now, for me and for our international customers, the cut and the feel of the fabric, the texture, are paramount. Those are the most important things for us now.
When you are in the design stages are you taking into account what your customers are asking for or what you think that they might want?
Of course, yes, we are doing that. So in Japan right now let’s say that there’s probably…let’s see…of the well-known ones we’ll say there’s about 10 denim brands all doing their own thing. So for example, Iron Heart appeals to those who like bikes, Samurai to those who want super tough and heavy jeans, Warehouse appeals to the guys who are into the vintage stuff so…even within the Japanese denim niche, it’s kind of divided itself into several different categories. For PBJ, I think we fall into a category of “Japanese” Japanese jeans, if you know what I mean. We don’t make replicas. Our strong point is our rough, slubby fabrics which our customers have now come to expect from us, so this is how we make our fabric every time. The other thing is our natural Japanese dyes. Within these two parameters though I have an open mind with what we create.
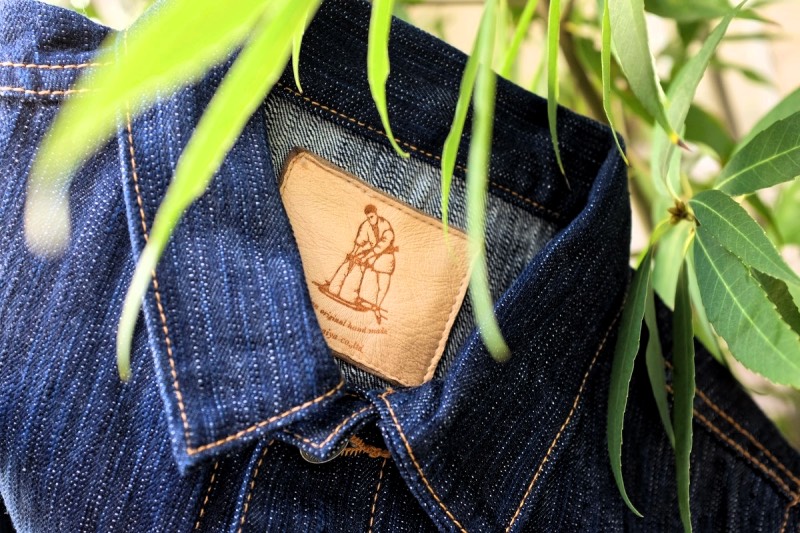
Aside from your own company, what other denim brands do you like? Maybe ‘like’ isn’t the right word, but maybe ones that you appreciate or respect what they’re doing?
Well we’re all doing different things, but for brands that I can really say, “Wow, those guys are really good at what they’re making”, they would be like, Iron Heart, Full Count, Warehouse…Real McCoys. Their attention to detail and no-compromise approaches are really impressive. The types and styles they are making are of course really different from what I’m doing but…I think they are awesome at what they do. But to be honest, I purposely try and not look at what the other brands are making you know…sometimes if you see something really good it kind of gets stuck in your head and you can end up unconsciously copying it in some way in your own work. All those guys, we all get along well with each other, attend the same exhibitions but…yeah, I purposely don’t look at their stuff.
So you don’t really feel any kind of rivalry or competition between the brands then.
Hmmm…well we are all in the same business of making jeans so I guess there is some sort of natural rivalry there in that sense, but I don’t think anybody is trying to copy anybody else’s designs or undercut anybody else, like producing an identical item and then trying to sell it for cheaper than the next guy. Nothing like that. I think everybody is motivated by each other to improve their techniques and their jeans, and of course as businesses we want to be able to sell our stuff, that’s just natural. But no, nobody is trying to copy or steal business away from anybody else.
That sounds good actually. Do you have personal favorite jeans or fabric that you’ve made up until this point?
Yeah, the 14oz slubby fabric we’ve been making for a long time…and also the heavier 16oz fabric we’ve just been doing more recently, both of those. Our specialty is the neppy, rough fabric so… Another thing is our fabric that uses indigo in both the warp and the weft, something that nobody used to do, that’s also been popular for us.
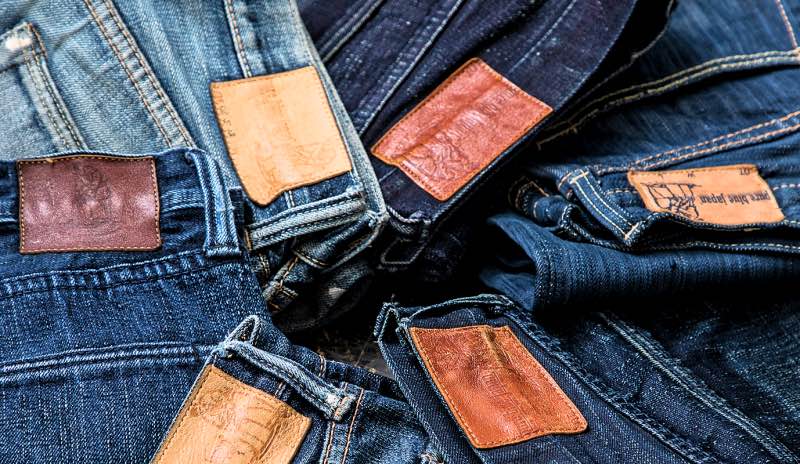
The next thing I’m sure everybody wants to know is where your fabric actually comes from…
It’s from Ibara (small city in Okayama).
Cool, so it’s not really a secret then (laughs). Wasn’t sure how you’d answer that one.
Everybody knows. Well, I mean, it’s a different matter if we’re asking the average person on the street if they know where everybody’s fabric comes from, but among us (denim brands), it’s pretty much known. I know where every maker’s denim is coming from…probably even which individual looms it’s coming off of.
(laughs). Wow, okay. I guess you use several mills in Ibara?
Well there’s not that many even existing there now. Not counting the mills that have trainees working at them, the mill that does the very best weaving possible…everybody is mostly there. It’s not like each denim maker uses a different mill – in this case, within the mill there are a lot of looms so it’s like these machines here are for Brand A, these next however many machines over there are for Brand B and so on, like that, within the same mill.
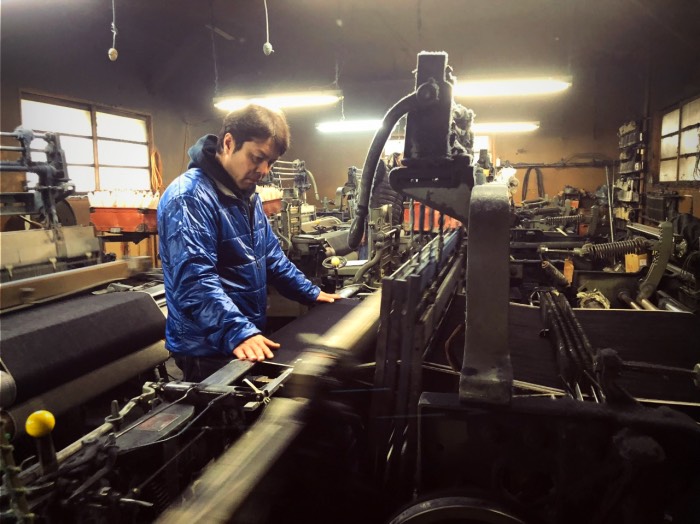
Photo courtesy of Okayama Denim
So what is the relationship between you and the mills? Are you always in contact, or going there in person to check how the weaving is going or….
Well it’s a bit different for me because, as I mentioned earlier, I used to work with the mills even before I made jeans so I’m close to them from those days. But it’s not as simple as it just being me and them – there’s a third person. Weaving is a job in itself and making jeans is a job in itself. But between us another job is needed, somebody who deals with the threads and all the preparation that is required before weaving can even start, so the three of us are always talking together, in the mill. So I would say, “I want to make this type of fabric. Do you have the threads that could do it?” And he might say, “No we don’t have that” so then I’d have to see if he could make me that kind of thread, ask how long it would take, when could I see a sample, etc. So we need to start with detailed conversations like this.
Okay, so the thread guy is also a very important link…
Yes, and if you’re going to go ahead and a make a fabric you can’t just make a little bit, you have to make a lot at one time, so of course we first need to see samples beforehand and then make sure we actually want to go ahead with that particular run of fabric. Each year we probably do about 50 sample fabrics, but we might only go ahead and actually make maybe 10 of them. Even if you’re using identical thread, you’re always playing with the thickness of the warp and the weft, the tension of the weave, and we can’t go ahead until we can really confirm the texture so…samples are super important and we need a lot of them.
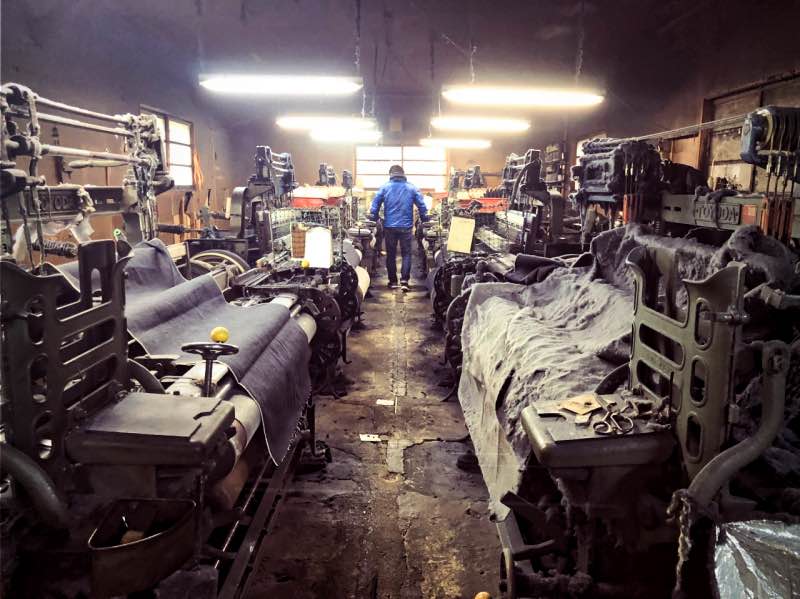
Photo courtesy of Okayama Denim
Wow, that’s way more complicated than I imagined. Interesting. Can I ask if you think that the future of Japanese denim might be in trouble because of the lack of weaving mills, the old machines, the lack of people that can run them and fix them….
I think the fabric side of things will be fine. To be honest, the reality is that denim is essentially made by machine. Yes, you need somebody skilled to run the machine and fix it, but basically the work itself is done by the loom. The bigger worry is sewing. The people who sew the jeans. This is completely done with their hands, and these people are getting older, mostly all over 60 now. There are currently some people from overseas training and learning how to do this in Japan, but again, even the Japanese people that are teaching this are getting old. Also, not all sewing factories are at the same level – some are good and some are not so good.
Right. That makes sense for sure.
Another important factor is how good are the actual machines in the factory? The machines we use are old but highly customized with different attachments added with the intention that even if different people use the same machine, they can produce a good product. But now even the people who are actually able to customize these machines are disappearing. Even if you go and buy a brand new sewing machine, you can’t just go and make good jeans with it. So we have to customize everything, so it can go through really thick material for example..that’s the most important thing, the customizing of the sewing machines.
I see. Again, not something I would have immediately thought of.
For example, I was showing you how our jeans have really long stitches…that’s only possible by seriously modifying the sewing machine. It would be impossible otherwise. And the people who can do that are mostly gone. That’s the biggest problem we face. More than making fabric, sewing is going to be the issue.
Where is your sewing actually done?
In Hiroshima, Okayama, and Tokushima. We do it in 3 places.
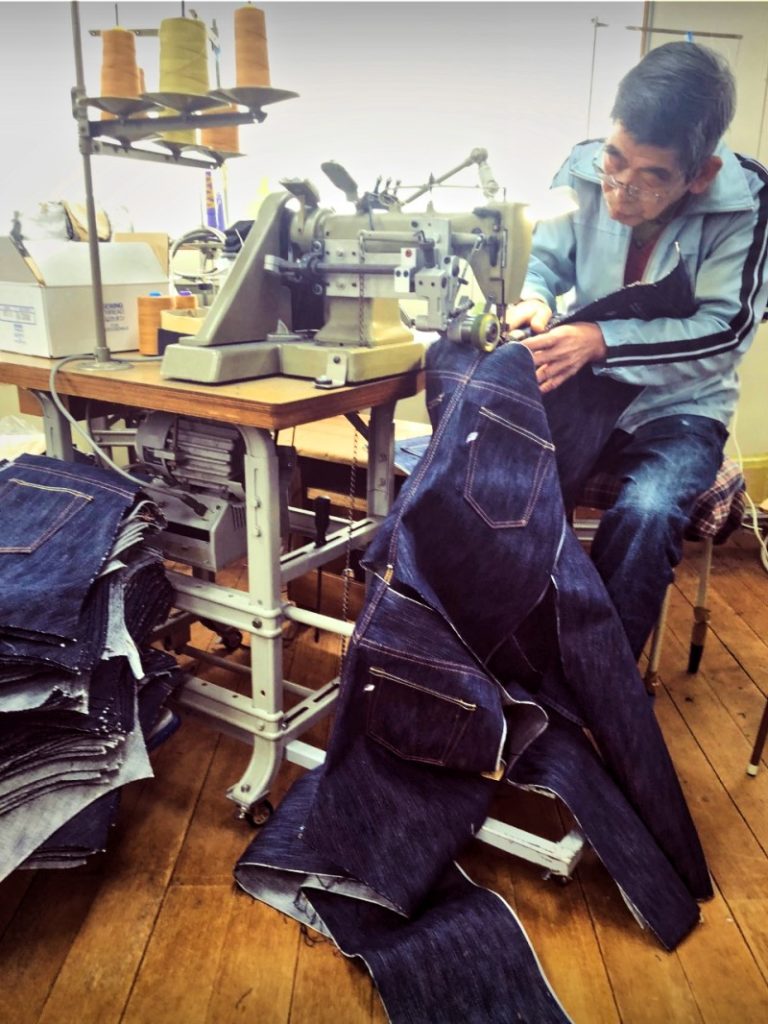
Photo courtesy of Okayama Denim
I’ve heard about ‘Kakishibu’ dyeing and I’ve seen the jeans, but could you explain a bit more about that? It’s actually from persimmons?
Yes, exactly. The fruit is crushed and you get this liquid and the threads are dyed in that. Long ago it was just like indigo in that it was used for its insect-repelling qualities. To be honest though, if you just wanted the persimmon orange color alone and that was enough, then you’re better off to just use a cheaper chemical dye of that same colour, but you know, nowadays there are a lot of people who love to use natural products, so we use real Kakishibu from persimmons.
And whose idea was it do that?
Well, Kakishibu has actually been around in Japan since long ago…
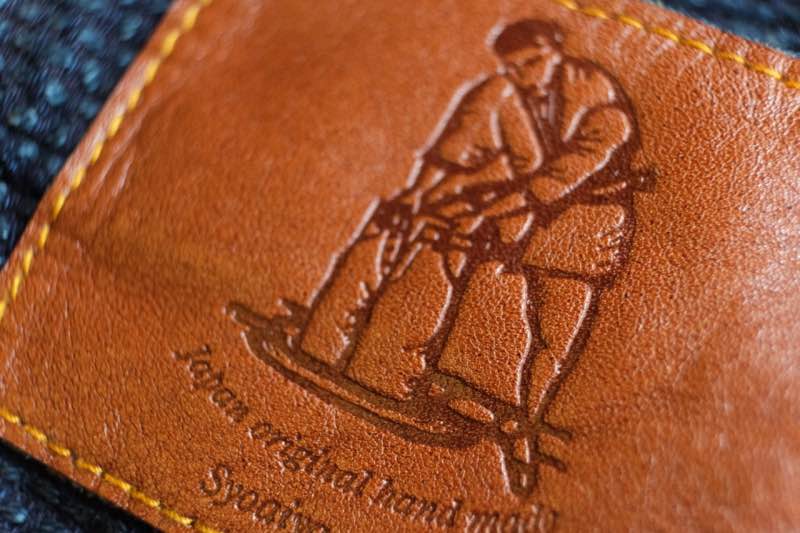
Do you get a lot of customers from overseas coming in to your shop here?
Yes. A lot. I’d say about 85% of the people that come in are from overseas.
Wow, that many? From where mostly?
The States would be the biggest.
So what do you do when customers come in and speak zero Japanese?
Well I’ve been selling jeans overseas for 12 or so years now so I can speak enough in English to at least talk about jeans in the shop. At the start I couldn’t at all, but now…I can’t really understand or have a difficult conversation, but for explaining about jeans in English, I can do that. I still have to go to exhibitions overseas twice a year, and at the beginning I used to hire a translator for that, but these days I just do it by myself.
What are some differences between your overseas customers and customers in Japan?
They’re different. It would take me a while to really answer this one properly, but, the stuff we are making isn’t cheap, right? The whole boom was about 25 years ago so people who are over, maybe 45, feel that these prices are normal for the quality. They probably bought expensive jeans when they were younger, and though they’ve probably gotten married in the meantime and can’t necessarily go out and buy them now, at least they see the value in them. So I think a lot of the people here who can really appreciate the quality and what goes into making these kind of jeans are generally over 40 or so.
Old fellahs like us….(laughs)
Exactly. Young Japanese people these days aren’t really into buying expensive clothes, no matter how good the clothes themselves might be. There’s a lot of young people here who, even though they might desire something, they just say like, “I don’t need much money to just get by in life”. In the past in Japan it would be people who had a lot of extra money or were just truly into our jeans that would buy them so if there was another boom here then of course we would grow but… This is why we started to sell overseas. So obviously there are a lot of people in the world and even though those who have income to buy things like this are probably small percentage-wise, that small percentage is still a large number of people. So about 15 years ago we decided to give the international market a try. But of course overseas too, naturally, most regular people would be like, “I don’t need stiff clothes like this.” But luckily there are also those people who do want what we’re making.
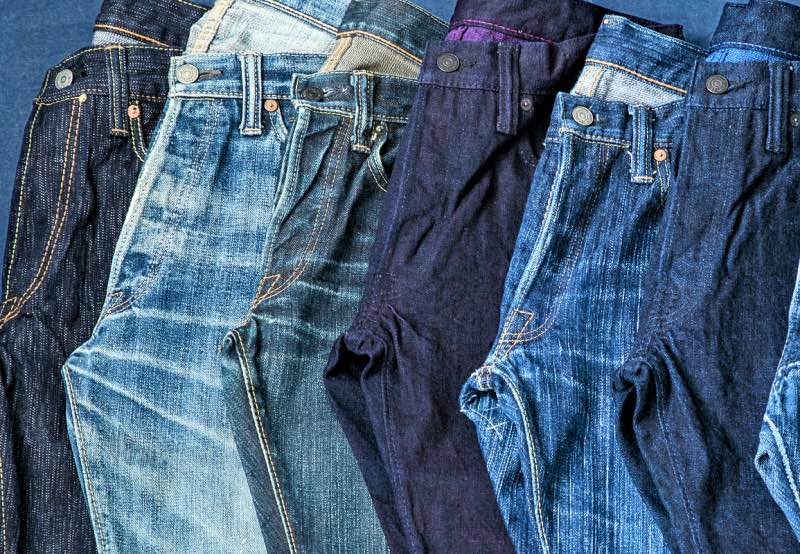
Photo courtesy of PBJ
Do you see particular differences between what your domestic and overseas customers want?
The customers from overseas care a lot about the cut, probably more than in Japan. I find that they also are more interested in the story behind how something was made and they don’t mind if something takes time to make; they would be willing to wait for a quality item. They want to know who made it, how it was made. Many Japanese customers tend just to look at the finished product and decide if they like it or not, as it is, without really caring about how it was made or thinking too far into it.
What’s the best part about your job?
Well it’s more than a year from when we start making new fabrics to when the customer actually sees the finished product so…you know, that whole time we’re making something that nobody has seen. And this whole time I don’t know if they’re going to sell or not so we’re kind of running blind in that sense, but we still have to go ahead and make all the fabric and then do our work as well as we can without knowing how it will be received. So when we finally release the finished product and our wholesalers or customers finally see it and like it, that’s the best part of the job for me.
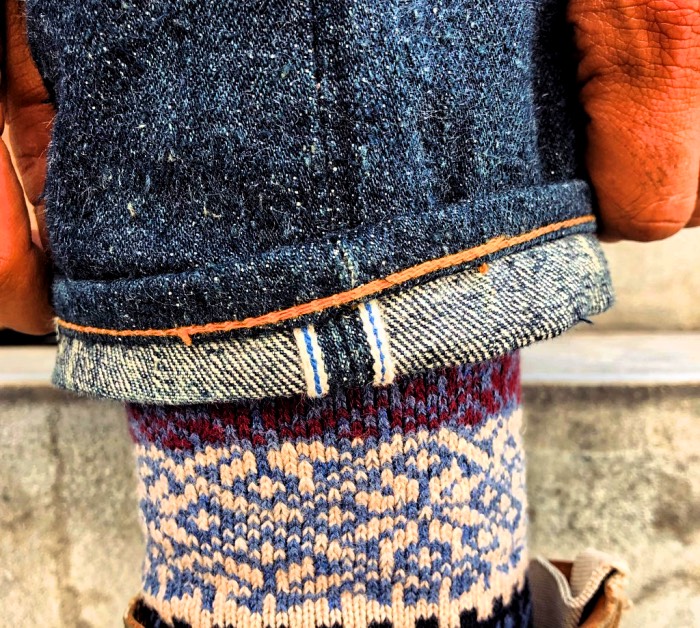
Photo courtesy of Okayama Denim
I can imagine that. How about things that are tough about your job?
Well firstly, you never sell every last thing that you’ve made. Also the stuff that we make isn’t changing into something else with every new trend or fashion like some other types of clothing. Denim is a niche market and then there are niches even within that. Like the other companies, we’re making denim of course, but we specialize in Japanese indigo. It’s a pretty specialized part of an already specialized market, pretty narrow, but still we have to come up with new ideas within that, for our customers. If you just lined up different kinds of denim beside each other, they do look similar for sure, you’ve really got to feel them to find the differences. But we still need to be constantly making new stuff within this narrow niche, and that’s a challenge for sure. I can’t just say to everyone, “Hey sorry guys, I just couldn’t think of anything good to make…too bad, but nothing new this year” (laughs). That just wouldn’t go over very well.
Yeah that does sound like a huge challenge. Next question might also be a challenge (though not as large as the one you just described) but…what kind of guy are you? How would you describe your personality?
I’m a pretty dry person.
Dry?
For me, things are a yes or a no. I either like something I don’t. I don’t make things I don’t want to make, I don’t sell things where I don’t want to sell things…
Black and white.
Exactly.
Well that’s not so bad. It’s good to be honest and direct I think. So aside from making clothing, what else do you like to do? What makes you happy?
I love making things. Food…I love just zoning in and focusing on doing one thing…even the ‘chok-chok-chok’ sound of the sewing machine when I’m working. You know, making food takes time, right? I like to just focus on the process.
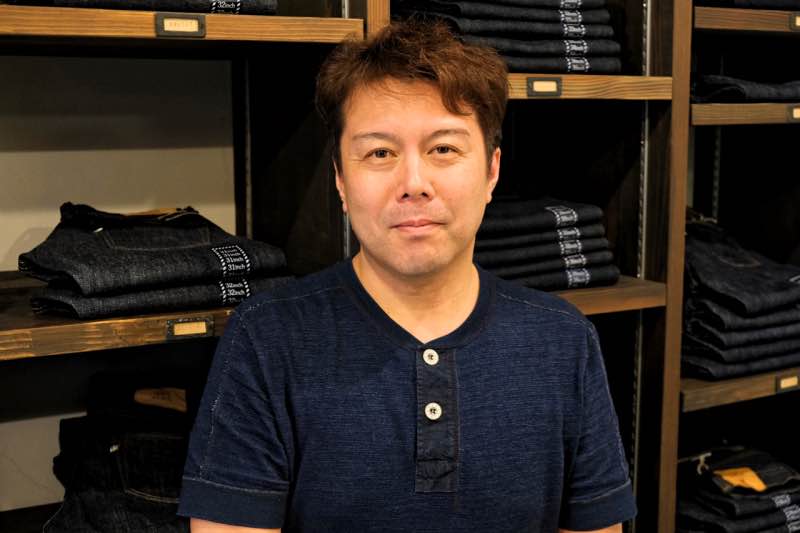
I’m like that as well actually. Moving on, is there anything we can expect from PBJ in the near future, like any new items, cuts, fabrics?
Well I’ve decided in my mind that, as far as the jeans go, I will create at least 2 new fabrics every season, so I’ll continue with that as I have been.
So can I ask how you actually do that? I mean how do you just ‘make a different fabric’? What is the process you need to go through to do that, and how are the fabrics different each time?
Mmm…well, what we’ve been doing lately is…if I just explain it in a general sense, one of the main differences that you’re going to notice between different fabrics is the weight, light, heavy…and how the thickness feels to the touch. And then hue, lightly-colored, dark…these are the things you’ll notice by how the denim looks and feels. The next thing is the texture, how it feels. It’s all from the thread, we make all our original thread and this where it all comes from. If we don’t do everything properly from the start like this, our stuff won’t be that great…it’ll just be another thing that anybody could make.
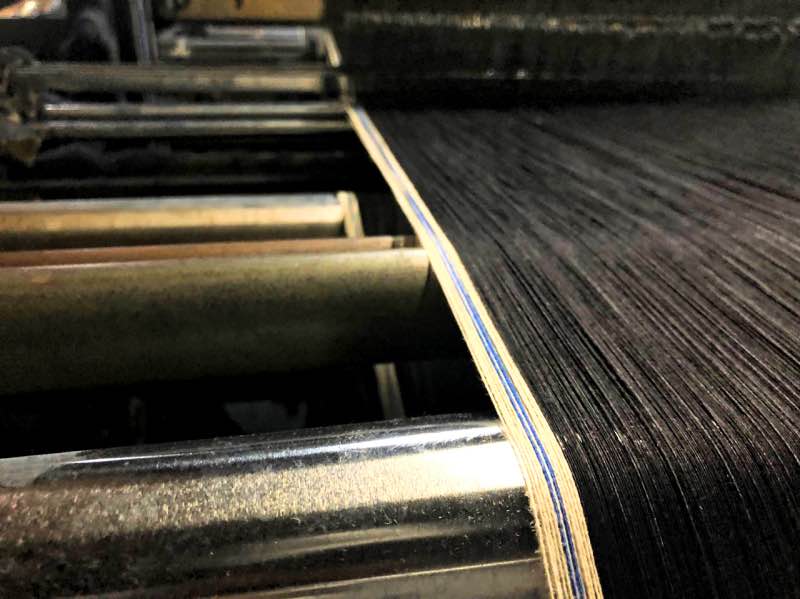
Can you talk a little bit about the differences between natural and chemical indigo? I know the price is quite different, but what else is going on there?
Yes, so there’s chemical indigo, and then there’s natural indigo, but there are actually two different types of natural indigo. The type of natural indigo that we are using comes from Tokushima (a prefecture on the island of Shikoku, off the coast of Okayama). This indigo is grown from seed, the plants raised, harvested, fermented like that. That’s the natural indigo we use. It’s expensive, and the dyeing has to be done by hand, not machine. This dye costs a lot and takes time to create and use. Then there’s another kind of natural indigo that is produced in large amounts in places like India. They also have a long history with indigo of course. This indigo is powdered and then exported and is meant for rope dyeing so you can use a machine. This imported powder dye is way cheaper. That’s why the price of our natural indigo jeans is higher than our regular ones…but that can be hard to explain to people!
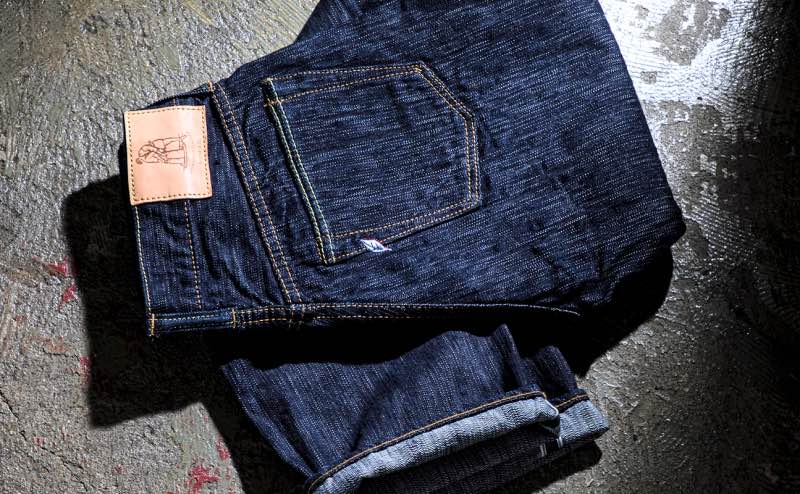
Photo courtesy of PBJ
Alot of people talk about the glory days, the denim boom back in the 90s. Do you think nowadays the denim industry is kind of heading downwards, upwards, or just trundling along more-or-less in a straight line?
Denim is just one niche industry so, at the very least, there’s no way it’s going to suddenly explode and go way up. I think one of the differences between now and the denim boom here 30 years ago is that at that time it was just contained within Japan. And that has actually really been the case up until relatively recently. I think recently, within the larger fashion world, ‘Japanese denim’ has become it’s own category. That’s meant that there are a lot of people in the world now who know about Japanese denim and know what it is. Also, because what we do is such a niche thing, there’s no way the huge fashion companies here are going to get into it with us so I think all of us small companies will be able to continue just as we are into the future. Like if UNIQLO suddenly was like, “Hey let’s drive out all the fabric companies and take over the mills!”, wouldn’t we all just disappear together? Even if they did do something like that, where are they going to sell all that? They can’t and they wouldn’t. Even though UNIQLO does make some cheap selvedge jeans, they aren’t something that the average UNIQLO customer is screaming to have. So I don’t think people like us are going to disappear. But we’re not suddenly going to break out either. We’ll probably just continue more-or-less as we are now.
Some people complain that the inseam isn’t long enough on Japanese jeans, that they’re too short.
Hmm..well I wonder how long they should be then…we do make them in 35 inches now.
How about the complaints that the pockets can be too small or the openings too tight?
Well they’re made in Japan by Japanese so…we have small hands. I think that’s one reason.
How do you strike a balance between staying true to traditional production methods while still continuously coming up with unique products.
Mmmm…well I don’t think that tradition is something we necessarily need to lose, you know, like now we have these old shuttle looms banging away, making our fabric. But even still, and this is connected to what we were discussing earlier, if you had the money it’s actually possible these days to just get a modern, computer-controlled loom and make similar fabric way faster. You can actually just push a button and still get really slubby fabric…this is totally something you could do if you wanted…but there just isn’t that kind of demand or place to sell that much when we’re already making denim the traditional way, so nobody does it right now. That’s one aspect of it. There’s also that…more than just making things, if there are no machines to make them with, then there’s nothing we can do. So I don’t think that our stuff is good only because it was made on old machines. To give an example, if you think of it one way, the reality is that a Toyota Prius is actually faster than a vintage Ferrari.
Yeah I suppose that is true. I’d take the Ferrari though.
For sure, but the point is that even though I know exactly what I want to make, it doesn’t absolutely need to be made in an old-fashioned way. I mean that’s how we have been doing things up till now, and the people doing it have been doing a good job, but if you consider what we were talking about earlier, that the machines are getting more rare, the people who can use them and fix them are disappearing…we can’t continue this way forever. I think with this being the reality, makers like us should really start thinking about ways to continue making what we are making, but using modern equipment. It’s a reality we will need to face eventually, and something we should be thinking about.
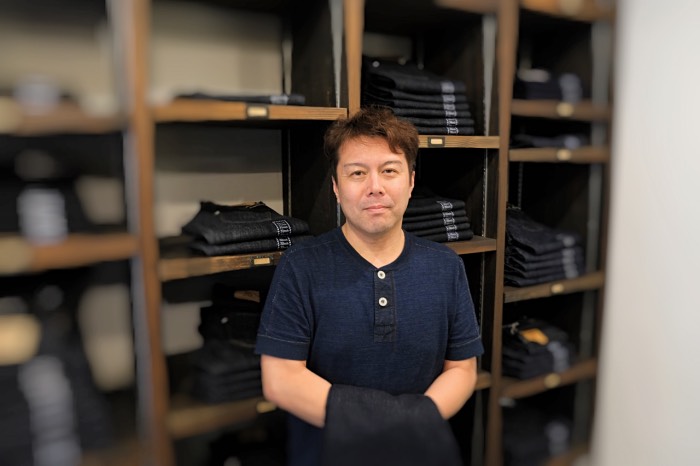
You mentioned earlier about the ‘long stitching’ that PBJ uses, and you showed me on those jeans…could you say a bit more about what that is?
(Grabs a sample pair to show me). So yeah, all of our jeans use large stitches like this. It’s actually harder than it looks to do them like this.
I can imagine. Is there a reason why you do that?
It’s for the look. With vintage jeans the stitches are super tiny and really close together, you can hardly see them, so we purposely made ours big and long just to distinguish ourselves from that.
Lately, some of the other Japanese brands are offering things like lifetime repairs on their jeans, or of course you know about Momotaro’s 10-year warranty. What is your take on this?
Of course having something that you can get fixed for free, forever, is a pretty awesome prospect for the customer, but to be honest, in reality, repairs can actually be a lot more difficult than even making new jeans from the start. It’s actually way faster to just sew something from the beginning. It’s incredible how much time it takes to properly unravel the seams in order to even begin a repair, so we do charge for repairs. This isn’t something we are trying to make money on; rather it takes a ton of time and work to properly unravel the seams, sew up every hole properly and prepare everything. We also need to take it back to the same factory where it was sewn originally. So what it takes to do these repairs and the job that we do on them are both probably at a level higher than what people might imagine.
Alright, I’d like to ask you about fades. Denim makers seem to have different takes on this, with some of them making that a high priority in the choosing of their thread and dyes, etc., while others are not really thinking about that, maybe just first focusing on making the best jeans possible and the fades will just appear as they will after the fact.
Well for fades in themselves, yes I do think they’re important, but with jeans, be it our jeans or UNIQLO’s jeans, they’re gonna fade no matter what. They’re gonna fade in some way or another naturally, but if you’re talking about the really high-contrast fades that people like then, yeah, best to wash your jeans as seldom as possible. I’m not sure if this is really a great example to use, but homeless people’s jeans have the most incredible fades. I mean seriously, they’re usually pretty amazing… (we both crack up and then collect ourselves) But of course jeans can get pretty dirty if you don’t wash them so… For me, I have to make good sample pairs of how the jeans fade for the customers, so for those ones that I want really standout fades for I just start wearing those ones in the fall. Then I’ll wear them through the winter, stopping when spring arrives. So when it’s hotter I just wear already faded out jeans like these ones (points to his very faded jeans) because I can just wash them anytime – they aren’t going to change any further. For us it’s also not enough to just say to our customers each season, “Hey guys, we made some new jeans…” People want know what they will look like when they fade, so we have to do that first, put up the fading pictures on Instagram. People aren’t going to buy our jeans if we didn’t do that, so yeah, in that sense too fades are important for us. You know, you can control somewhat how jeans will fade at the thread and dye level, but you’ll never know exactly how it’s going to turn out until you try it so…yes, I think fades are important.
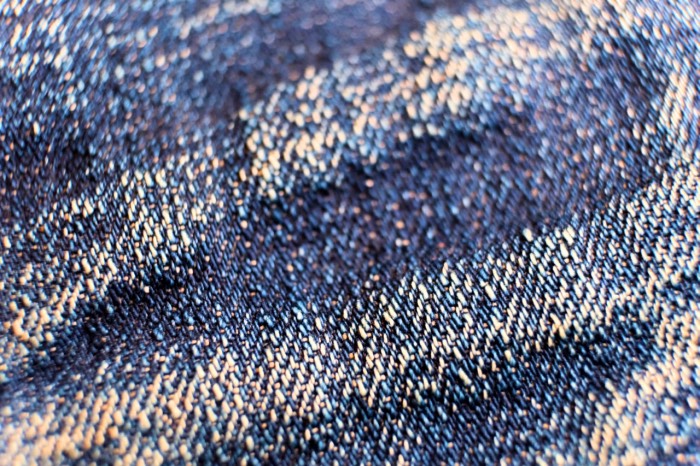
Next, I already know the answer to this but some people online were saying that you guys use just a single loom…that’s not the case it it?
No, we are not using a single loom. We’re not just at one spot. But there are cases where there might be a single loom somewhere that has been producing for us for a long time but…yes, we are using a number of looms. The types of fabric each place can produce are different, and each individual loom within one mill produces slightly different fabric even among the same type or brand of looms. So depending on the fabric we want to make, we use different looms.
And the people who can maintain these machines are decreasing.
Yes, they’re decreasing. Just like we were talking earlier about the people who can sew and modify the machines, it’s the same thing.
About the cotton itself, where does yours come from?
Ours is mostly from America. The main areas these days are basically the States, India, and China. The cotton from India was a lot softer than I had thought, whereas the cotton from the States has less moisture in it…it’s drier so I like it for the denim we make.
So you use the same cotton for all of your jeans.
No, we don’t, not always. You can’t just go and ask a spinning mill to make up some thread for you using whatever kind of cotton you want. Instead you would normally tell them the type of thread you are wanting and then their professionals will make it up for you, probably even mixing cotton types to get the thread you want.
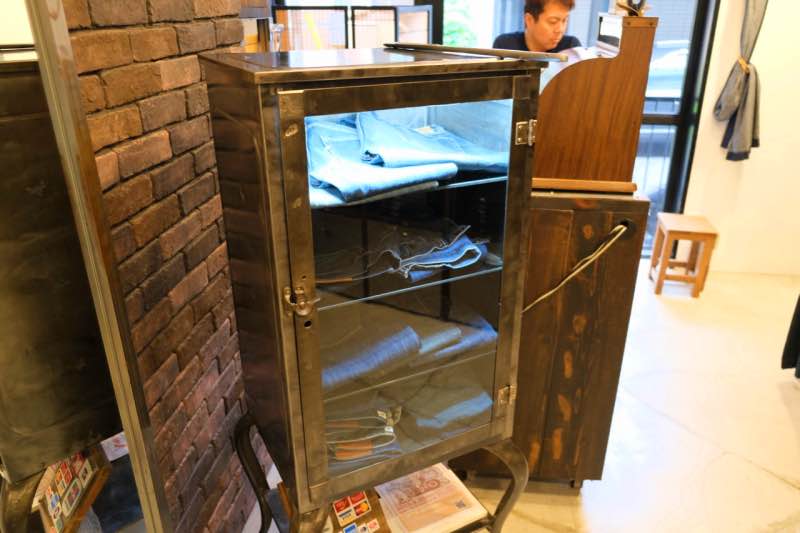
Can I ask why you guys closed down your Kojima store earlier this year?
Basically because we were too busy. About 10 years ago we started up there, and at that time there was only three of us: Pure Blue Japan, Momotaro, and another smaller place. And it wasn’t so serious at the beginning, I just kind of thought, okay maybe I’ll have a store and just open up on Saturdays to start…I just got into it lightly. That was 10 years ago. But since then, there has been a huge increase in customers from overseas and my job has gotten much busier, so the number of days that I wasn’t able to actually open the store was increasing. I did try to find suitable staff members to take it on, but it wasn’t easy. You know, if you have low-level staff working for you, the whole company kind of drops in level too. Really good workers like the two I have here now, I just couldn’t find anybody like them you know, so…I just figured isn’t it better just to close the store? So now I just have the Tokyo Harajuku shop along with the head office in Kojima where we do the shipping. I know it’s never a good look to shut down a store, but I was just too busy to do it properly.
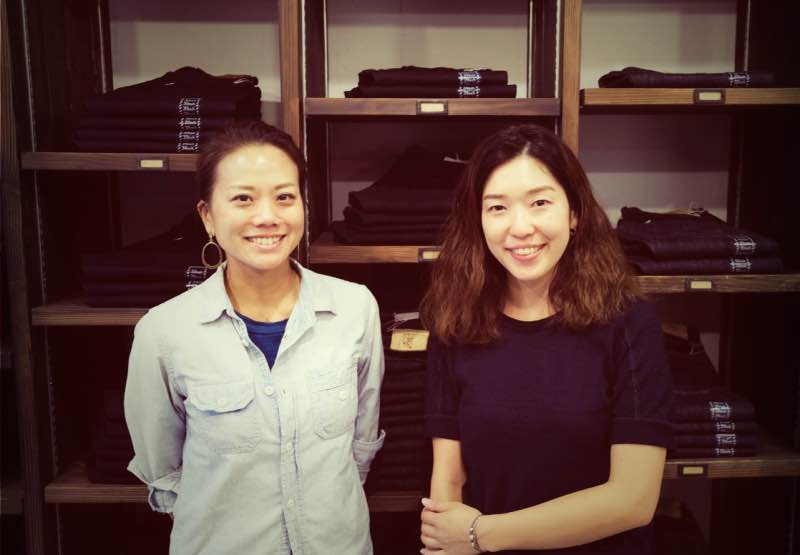
What might a typical work day look like for you?
I would normally head to the Kojima office about 8:30, check the mails, etc. It’s mainly shipping, visiting the mills, and going to the sewing factories. I do those three things pretty much every day.
So how often do you come up here to Tokyo?
If there’s stuff to do, then I’ll come every week. If there’s nothing I need to get done here, then I don’t come up.
Every week?
Yes, there’s things like business talks or information stuff like we’re doing now, later today I have agents coming from Korea, one from Hong Kong…I come to meet our partners coming from overseas.
Are you planning on making more stretch denim in the future?
We’re making it at this moment actually.
What’s your personal opinion on the whole stretch denim thing?
Mmmm….(thinks for a while). For us it’s never going to be one of the main things we do. The people who are really into our jeans, their way of thinking about fabric is pretty set, you know like, “Selvedge has to be this way…vintage things have to be this way” kind of thing – lots of our customers are like that. And that’s totally fine. For us, stretch denim is made in the same way as normal denim, and it looks the same, except there is some stretch in it. And we are always after new ideas, coming up with new stuff. You know, they look the same as normal jeans and the feel the same as normal jeans and…to be honest they’re much easier to wear. So we’re making stuff like this now, like stretch denim, light summer denim, etc. I was saying earlier that Japanese denim has now become its own category in the larger fashion world, and while I don’t think we need to be serious into changing fashion trends like some of the other brands, it is still important to try new things and challenge yourself. But you know, we’re not going to sell a ton of it.
Are there a lot of Japanese brands doing stretch denim now?
Mostly all of the brands that make ladies stuff.
Lastly, I’m hoping a lot of PBJ fans will be reading this so is there anything you’d like to say in closing that we haven’t covered? Any messages for the PBJ faithful?
We are going to continue making our slubby denim and using our natural indigo dyes as always. We make all of our stuff here in Japan with no compromise whatsoever, so it would be difficult to drop the price of our jeans. Actually the cost of doing things will probably only rise in the future. But having said that, I am positive that our quality will never drop. I want to say too that in order to keep our quality so high, it sometimes means that deliveries take time. Of course I would like to be able to make more jeans more quickly, but that would be very difficult because we only use the few very best places to make our jeans. There might be Factory A and Factory B, but Factory B isn’t as good as Factory A so we just aren’t going to use them. If we did use more factories, of course we could make more stuff, but the quality would suffer. So we are limited in that way with how much we can produce because of the low number of factories we will use – two actually for our jeans and pants. Nowhere else could do it at the level we need. We also supply them from here with the modified machines they need. Our customers would notice any drop in quality immediately and there’s no way I’m doing that.
Wow…well I just want to say a huge thank you for all your time. This has been an incredible chat, we covered a lot. People are going to love it, getting to know you and the brand a bit better.
Really? That’s awesome then. You staying in Tokyo or heading home today?
Haven’t decided yet.
Haha…haven’t decided yet? Cool.
Thanks so much Iwaya-san.
Thank you too.
Visit Pure Blue Japan’s website here.
Special thanks to Okayama Denim for supplying some of the pictures in this article.
For a great hands-on review of PBJ jeans check out my man Nick over at Stridewise.
Amazing interview. He is just what I had pictured in my head in terms of philosophy and ideology.
Excellent interview informative and insightful.Thank you
Great interview. I stopped into the Harajuku store last year and was really impressed with the quality of the staff there. Super knowledgeable and clearly very dedicated to the products. The more years into denim I get, the more I love PBJ. There’s just something about their fabrics, cuts, and the clear dedication to detail in every pair and every shirt.
I love their stuff but they are not making size 40s and 42s like they used to.
Pingback: Pure Blue Japan Review: The Slubbiest Jeans on Earth?! - stridewise.com
Pure Blue Japan makes wehazt are by far my favorite denims, and the best indigo tees and sweats/hoodies as well. No onew matches the subtle textural and dye variations of their jeans or their knitwear. Their stubby tees are a special favorite, along with any of their Aizome offerings (both jeans and jackets. This is denim and dye artistry of a level that no one else approaches, in my experience. There are some very nice (especially the aizome) offerings from Momotaro, Samurai and Studio d’Artisan, but PBJ does so many special things – kakishibu (persimmon), pure indigo dyes, and their slubs are the most beautiful, producing bright highlights that are a thing of true beauty. Thanks for the indigo and other artistry.