Japanese jeans. Known the world over for their emphasis on quality, traditional production, and attention to detail, jeans makers in the Land of the Rising Sun are able to command premium prices for premium products, limited-edition models sometimes selling out within days or even hours of release. Japan, and Okayama prefecture in particular, have become synonymous with ultra high-quality denim, but when considered carefully, how much of your favorite pair of Japanese jeans actually originated in Japan? The hardware, probably, yes. And of course the denim itself was woven, cut, and sewn in Japan, surely making them ‘Japanese’ jeans. This is the conventional understanding of what makes a pair of Japanese jeans ‘Japanese’, and on the surface of it, it does indeed ring true. But something still didn’t sit right with Toru Nogami, founder of Osaka-based Samurai Jeans, as he and his friends waxed philosophical one night back in 2008 over what exactly would qualify a pair of jeans, or any other product for that matter, as 100% Japanese.
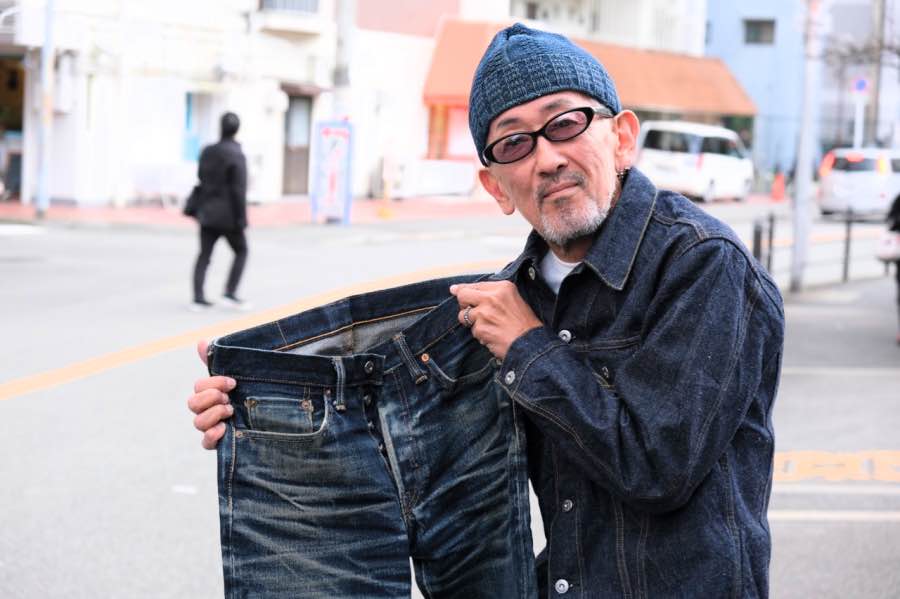
You would be hard-pressed to find a more ‘Japanese’ jeans brand than Samurai, with many their jeans taking their names and hardware design cues from people and events in Japanese history. Nogami-san himself had also assumed he was producing 100% Japanese jeans until it dawned on him over rounds of sake with some friends one fateful evening that that wasn’t really true at all.
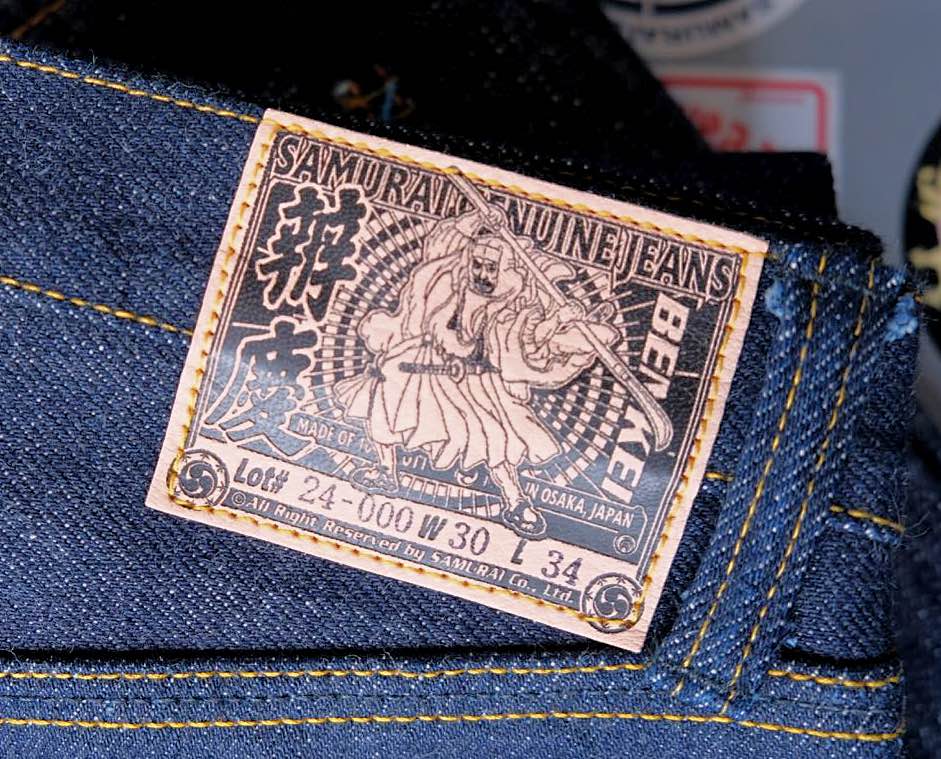
“There we were telling the world that we were making 100% Japanese jeans when really…jeans are essentially just made of cotton…none of which actually originated in Japan. So if a thing’s essence is what it’s actually made of, then we weren’t really making Japanese jeans at all. The material that makes up the jeans themselves is 100% imported. In that way of thinking, ‘Japanese’ jeans are really Texan, Chinese, Zimbabwean, wherever the cotton is coming from.” As the night wore on the statements grew bolder, with Nogami-san eventually stating that he would indeed set out to make 100% Japanese jeans. In the harsh light of morning however, it wasn’t clear exactly what that would entail, or how he might go about achieving such a feat.
Knowing obviously that denim is essentially cotton threads woven together, Nogami-san first set out to find thread that was 100% made in Japan, from Japanese cotton. He quickly found out that no such thread existed. Perhaps then he needed to take even a further step back and see if he could find some Japanese raw cotton that he could then have woven into thread in Japan, thereby enabling him to then weave 100% Japanese denim. Again, not much luck. This left but one option, albeit a farfetched one at the time: he would have to get into the dirt and grow the cotton himself.
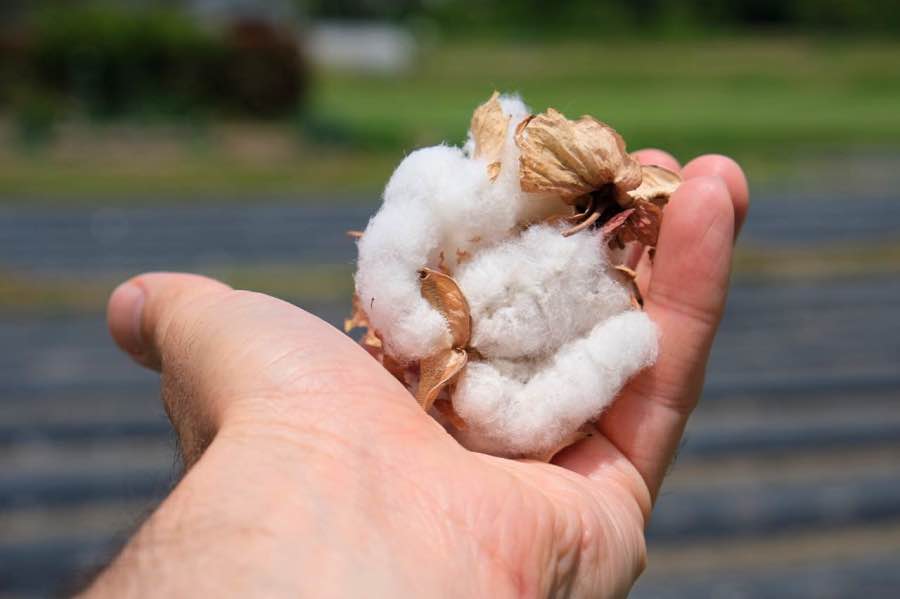
To say that this was easier said than done would be a gross understatement. Where to find proper cotton strains and seeds? Enough land to plant? Labor? Climate? And…how the heck was cotton grown anyway? Armed with little other than a dream and a whole lot of determination, Nogami-san sourced some Japanese cotton seeds, a small plot of land in Okayama, and set to work in the winter of 2008 trying to grow his own cotton. If the next part of the story were written by Disney, by 2009 we would have great, fluffy balls of cotton blowing on the wind, with all the happy inhabitants of the island dancing and singing in their newly-produced Japanese jeans. Disney, however, didn’t write this one.
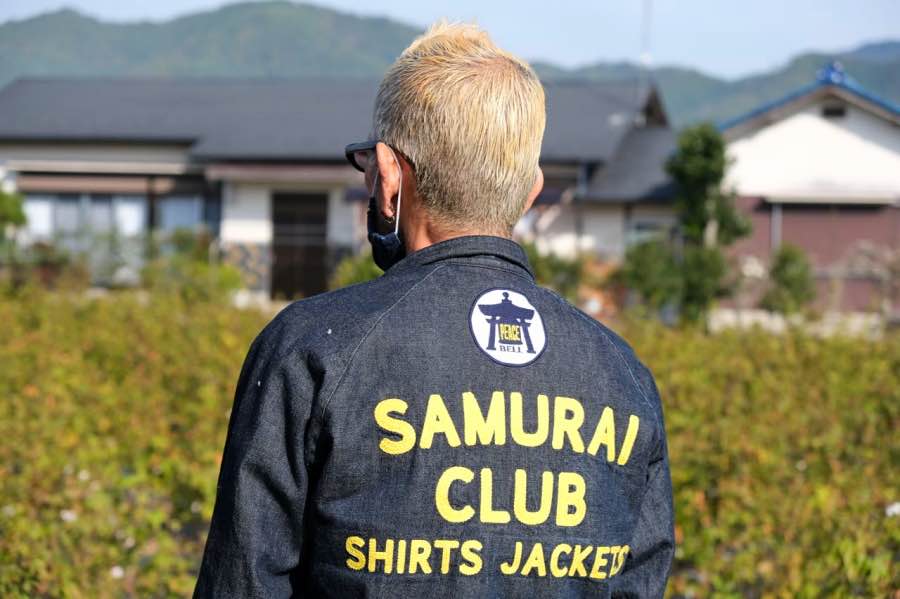
The first year or two was spent stumbling from one debacle to the next, netting the Samurai team precisely nothing in the way of cotton. Not one to lose heart, Nogami-san and the Samurai team pressed onward, learning from their mistakes, and slowly getting little wisps of white. After three years of trying, they changed location, moving from Okayama to a few abandoned fields in rural Hyogo prefecture.
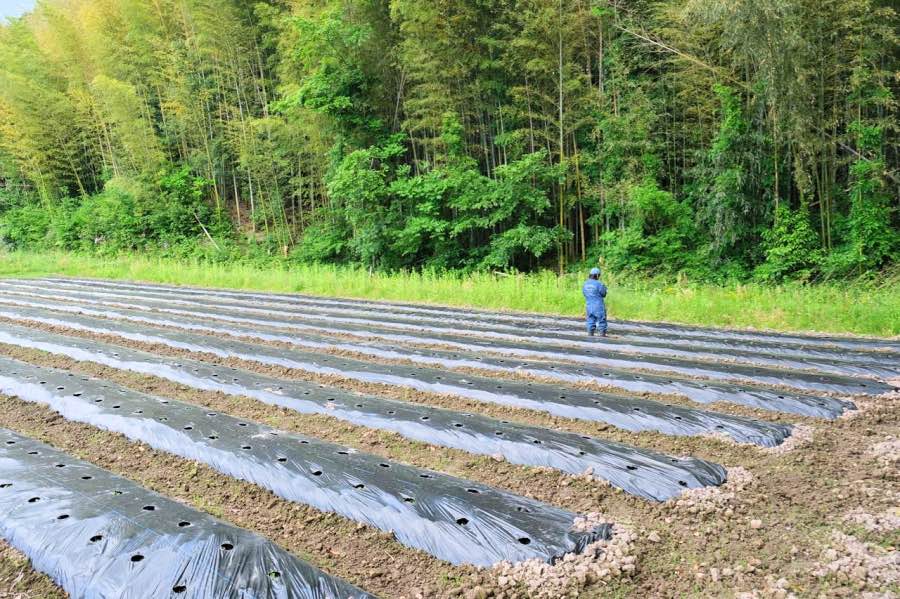
After years of effort, the team finally had enough cotton for a pair of jeans. A long-fought victory for sure, but Samurai main shop manager, Tao-san, tells of how, even having grown enough cotton for a pair of jeans, the obstacles were just beginning. Firstly, no spinning mill in Japan would spin such a small amount of cotton, with each mill insisting that Samurai mix their “wamen” (Japanese cotton) with imported cotton before spinning, firstly to increase the pitifully small yield, and also because Japanese cotton has such short fibers compared to most imported cottons, thereby making it very difficult to spin into thread on its own. As you can imagine, Nogami-san wasn’t going to mix his cotton with imported stuff. Not after all that hard work. Eventually they were able to find someone to spin their little bit of wamen, and then went in search of somebody willing to dye such a small amount of thread. They did eventually did find somebody to dye their thread, though it had to be done entirely by hand using natural indigo, not a cheap process by any means. All of these factors combined meant that the pair of jeans they produced was a little on the pricey side.
Most hardcore denim fans will be familiar with the infamous $10,000 pair of jeans that Samurai produced in 2013. I initially thought I had read the price tag incorrectly, but no, that is the actual price. Needless to say, that pair remains unsold in its intricately carved wooden box at Samurai headquarters. The price is more symbolic than anything else, and I don’t think Nogami-san ever thought he’d actually sell them (and part of me thinks he’s glad to still have them so close to home). On the surface of it the price seemed absurd, until to consider that it actually took them five years to produce a single pair of jeans. You read that correctly. Five years of time and labor for one pair of jeans. Suddenly the price sounded a little more reasonable. There was even an official ceremony to authenticate and commemorate the first pair of 100% all-Japanese jeans, and the huge plaque still sits up in the rafters at Samurai’s main shop in Osaka.
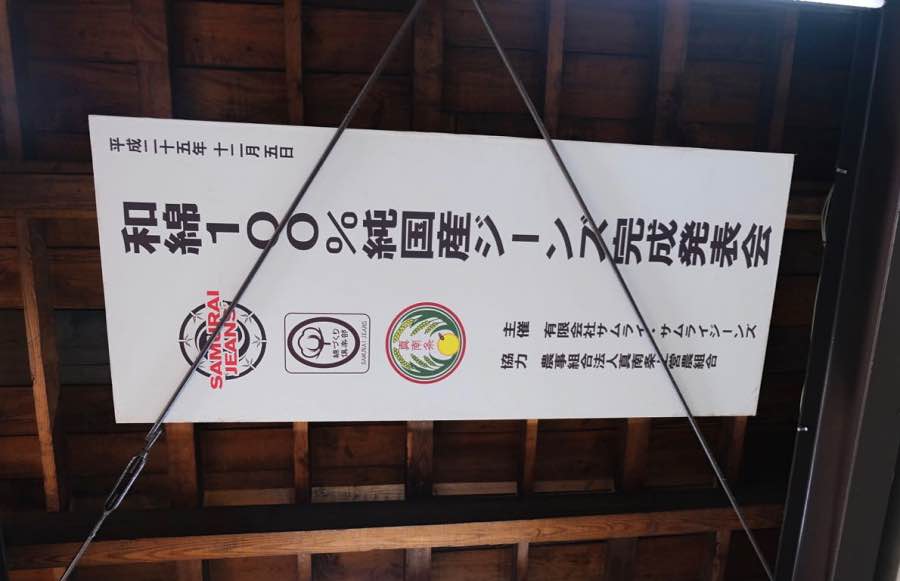
Fast forward to 2021 and things have grown considerably easier due to several factors. Firstly, the experienced gained over those early years taught Samurai how to properly care for the plants to maximize yield, though Nogami-san still insists that no chemicals of any kind be used. The plants are planted, weeded, and harvested all by hand (with bugs free to munch as they please). Samurai also now uses 5 or 6 small plots of land near Sasayama, Hyogo, and all work is done by a group of Samurai employees, a few dedicated customers, and a handful of friendly Sasayama locals.
To say things have gotten easier however, doesn’t mean that they are easy. Samurai still loses money on every pair, and it is literally a year-round love affair. If it’s just a money-losing venture, then why bother? I asked Nogami-san this very question as we sat eating our bento (lunch box) one sunny afternoon in Sasayama and he said, “It’s for the love of it. It’s not about money. In this one thing I want us to be unbeatable…to do something that nobody else is doing or has ever done.” Upon hearing that, I got that warm, fuzzy feeling and went back to quietly eating my bento.
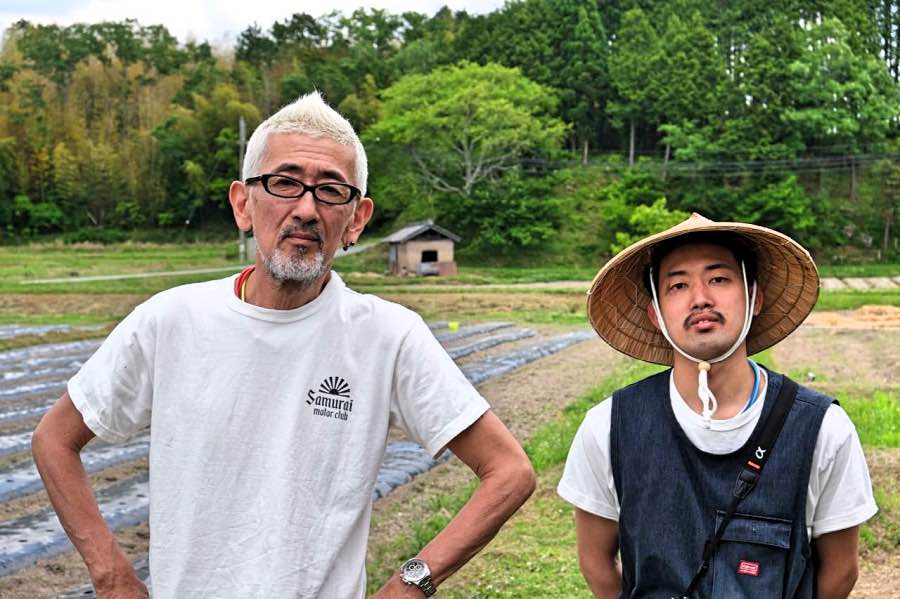
For the weaving of the denim itself, there is a heartwarming story that I’m not 100% sure I’m supposed to share, but I will. When Nogami-san first got the idea to grow his own cotton for his jeans, he confided in his friend, the owner of the legendary Shinya mill in Ibara, Okayama. The owner was so taken and excited by what Nogami-san wanted to do that he promised, should Nogami-san ever succeed and actually produce 100% Japanese cotton thread, Sato-san would weave his denim for him, no matter how small the amount. This might not seem like such a big thing, but as Nogami-san himself admits, “No place is going to even turn on a loom for such a small amount of denim so…that was really important and special. Unfortunately he passed away before I was able to produce enough cotton…so he never got to see that.” Fortunately, the wife of his friend continued running the mill and honored the promise her husband had made to Nogami-san, still weaving his small amount of local organic cotton into the beautiful denim you see in Samurai’s Cotton Project and Ai+ jeans.
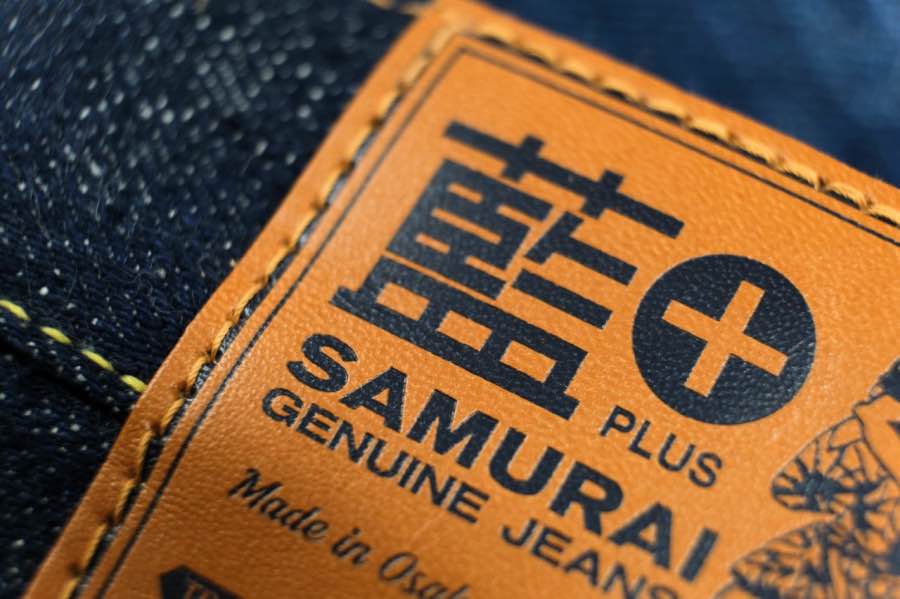
Needless to say, the jeans no longer cost $10,000 a pair. This is due to the fact that yield has of course increased, the thread is no longer hand-dyed, regular chemical indigo is now mainly used in place of natural indigo, and the jeans now use the Japanese cotton only for the weft, with the warp being imported thread. “Hey…wait a minute!” I can hear you say. “That’s not 100% Japanese! No fair.” But realistically, you aren’t going to go for long with a price tag like that, so Samurai had to make some concessions to reality. But to see the love and labor that goes into these jeans, I don’t think they are any less special for being “half Japanese”, and they are also now much more accessible to the regular (well, regular hardcore) denim fan. At best estimate, Samurai is now able to produce about 100 or so pairs per year that contain their all-organic, hand-cropped, Japanese cotton.
Work begins in the cold of February, the Samurai team and a small group of dedicated volunteers digging up all of the weeds, small trees, and previous year’s plants and burning them right there on the snow, returning the ashes to the soil.

The planting process starts at the beginning of May and can follow one of two patterns. Up until a few years ago, the previous year’s seeds were put into small pots and germinated in a greenhouse until they sprouted and were ready for planting. This again is a very labor-intensive process and couldn’t be done without all of the Samurai fans (some coming from hundreds of kilometers away just to help) who pitch in to get the thousands of seeds potted and germinated. Again, Nogami-san will only use JAS-certified organic soil for this important step.
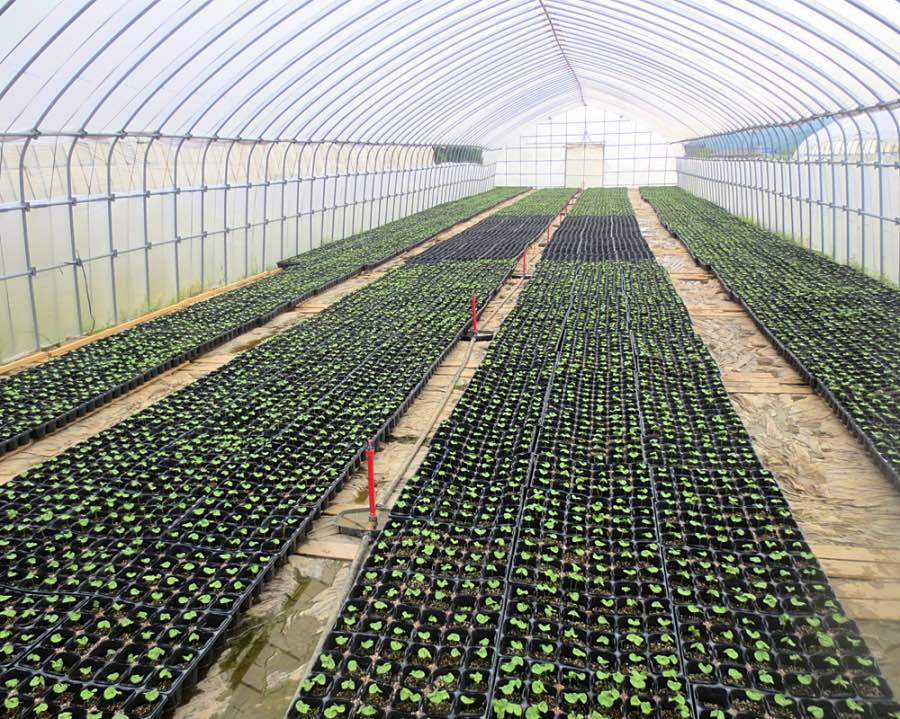
In the past few years however, as the number of fields Samurai has had access to has increased, they have moved away from this method and have begun instead to just plant the seeds directly into the soil. Nogami-san notes, “Of course seedlings have a much better chance of survival, but it’s also a lot more work to germinate them all in pots and rent a greenhouse and all of that, so we now just take our chances with planting directly.” Planting this way does mean that many of the young shoots will die or be eaten by insects, but Samurai tries to catch these early and replant them.
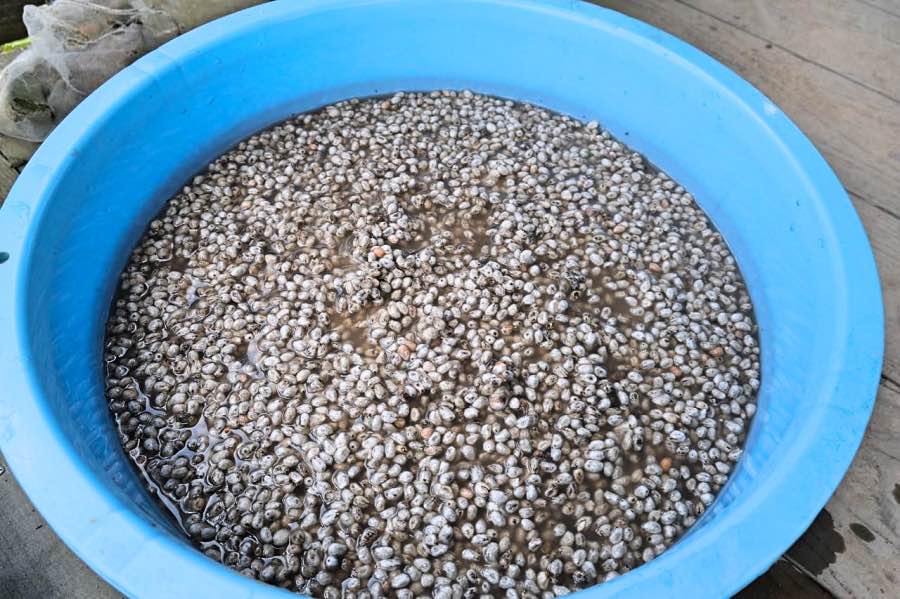
Planting itself starts at the end of May and can run into the beginning of June. Each seedling (or seed, as the case has been recently) is planted by hand, again by a combination of Samurai staff, keen customers, and energetic locals.
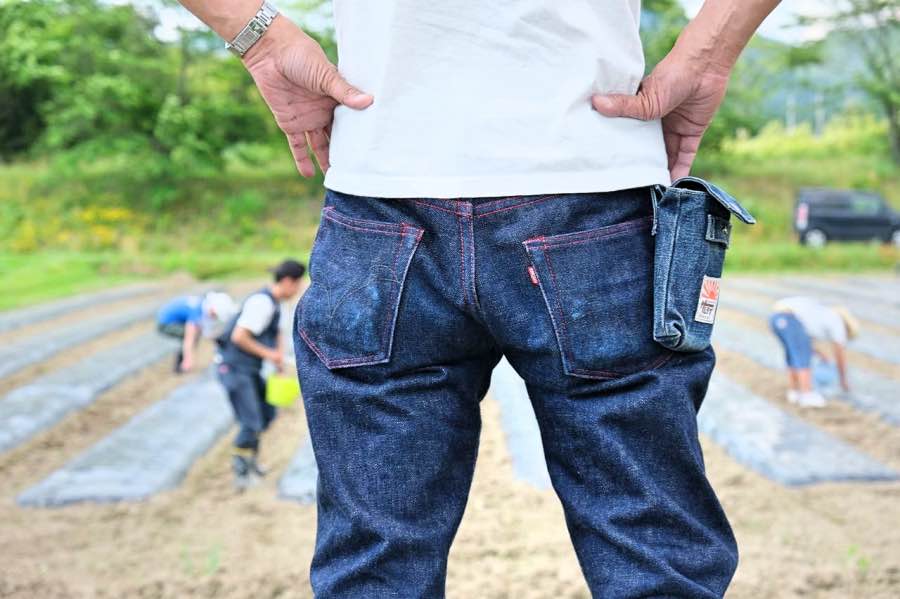
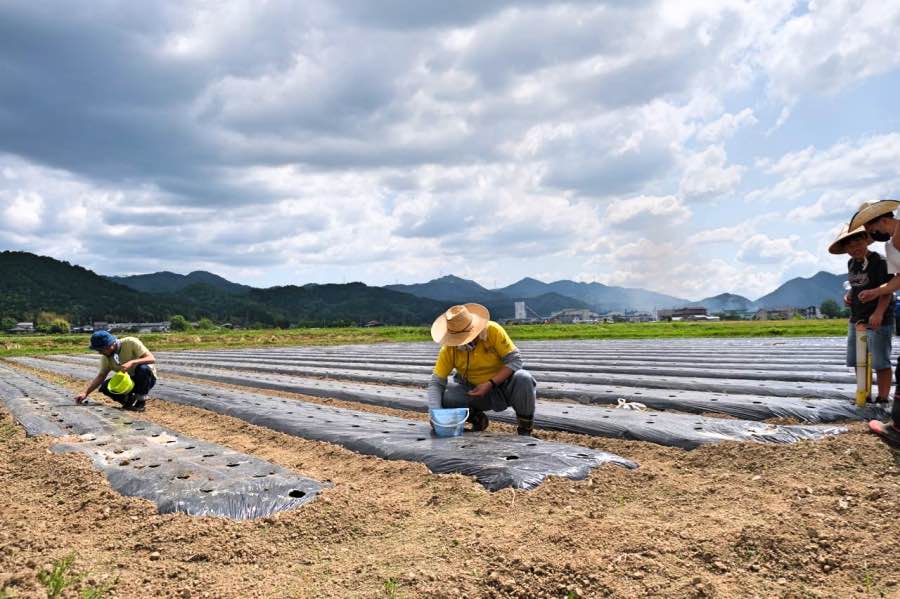
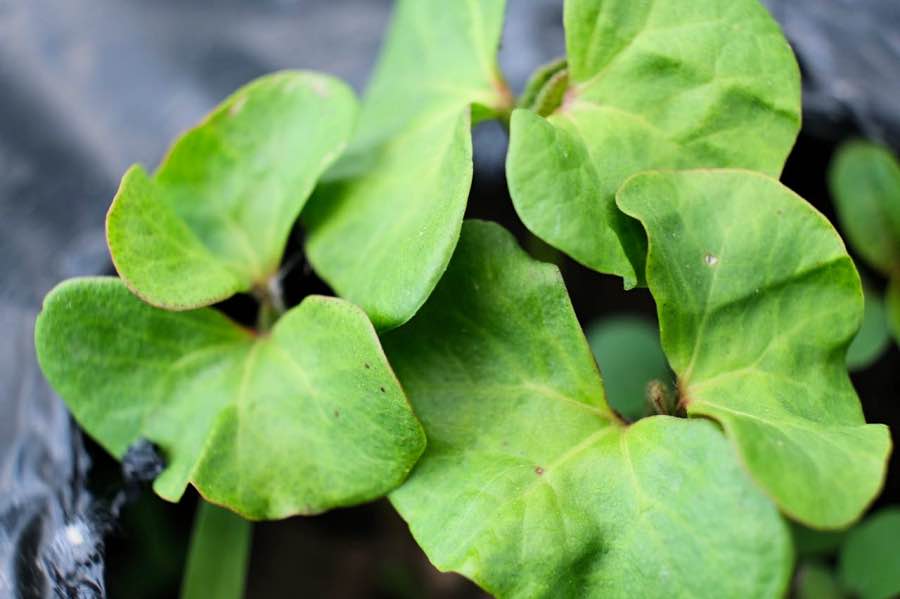
From June until October it’s basically a battle against the elements as grasses, weeds, animals, and insects of all kinds vie for space and nutrition in the tiny fields. Nogami-san refuses to use fertilizers or pesticides of any type, so teams need to head up to Sasayama (about an hour from Osaka) on the weekends to pull weeds and take care of pests. “It’s amazing how fast the weeds and grasses come in and take over, sucking all the nutrients out of the soil and essentially starving the cotton. A whole field can turn green with invading grasses in the blink of an eye. This is a much bigger problem than any insects.”
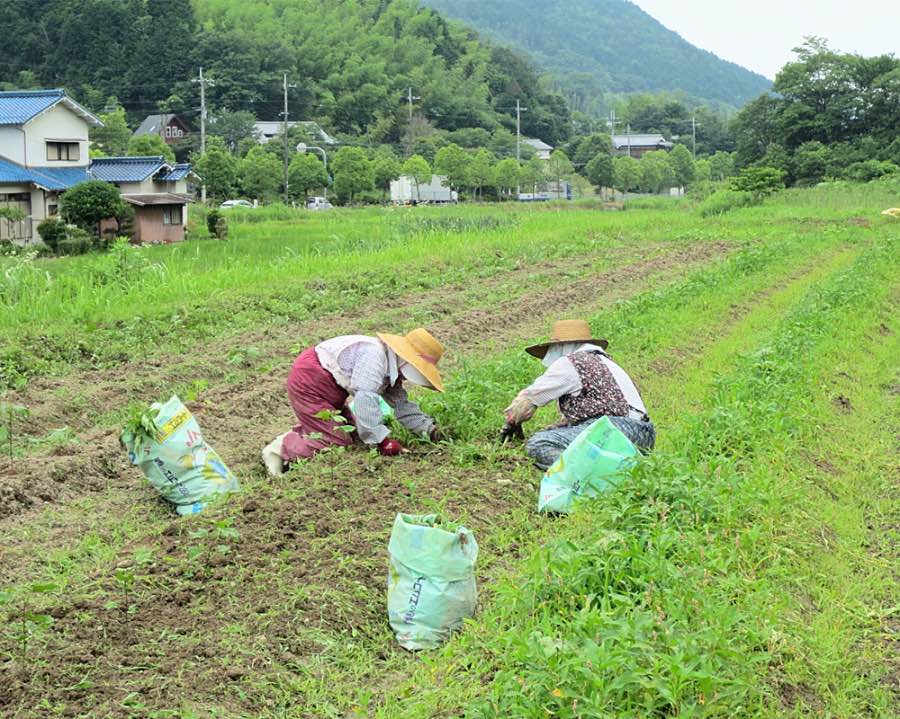
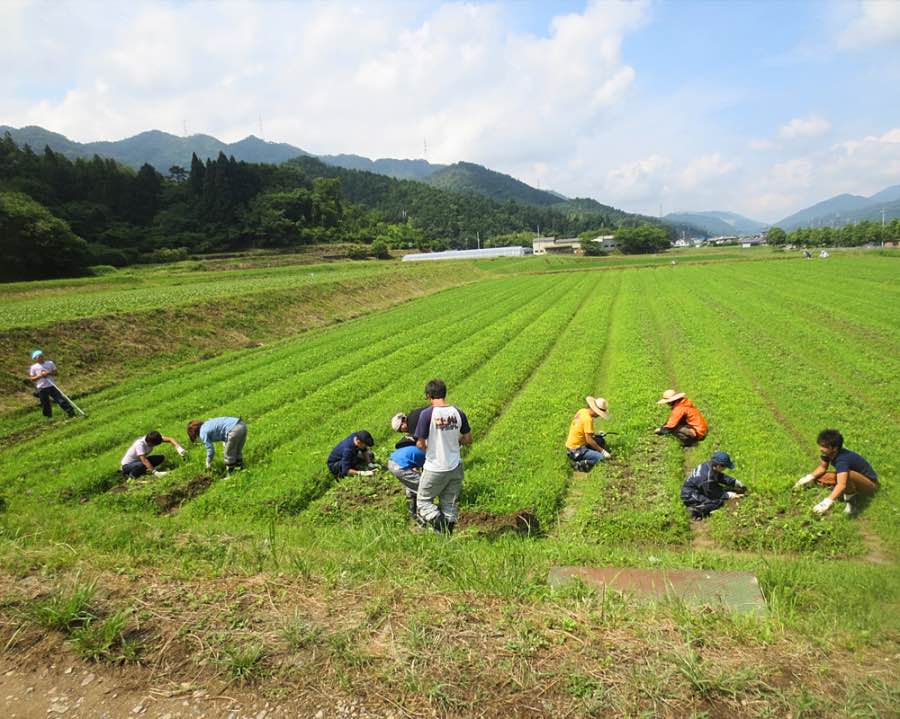
Then there are the seasonal typhoons that sweep through Japan and can level a field flat within seconds. Irrigation used to be done by hand, but after a few years, Nogami-san and the team discovered that the cotton did well even if they didn’t water it regularly, so now the only water the plants receive is whatever the heavens above decide to offer. If all of this sounds rather difficult, that’s because it is. But this in itself is very Japanese, the idea of coming through hardship as a group, making even a small victory all the more delicious. That is why Nogami-san sees each little fluff of cotton that actually makes it through to the October harvest as a precious jewel.
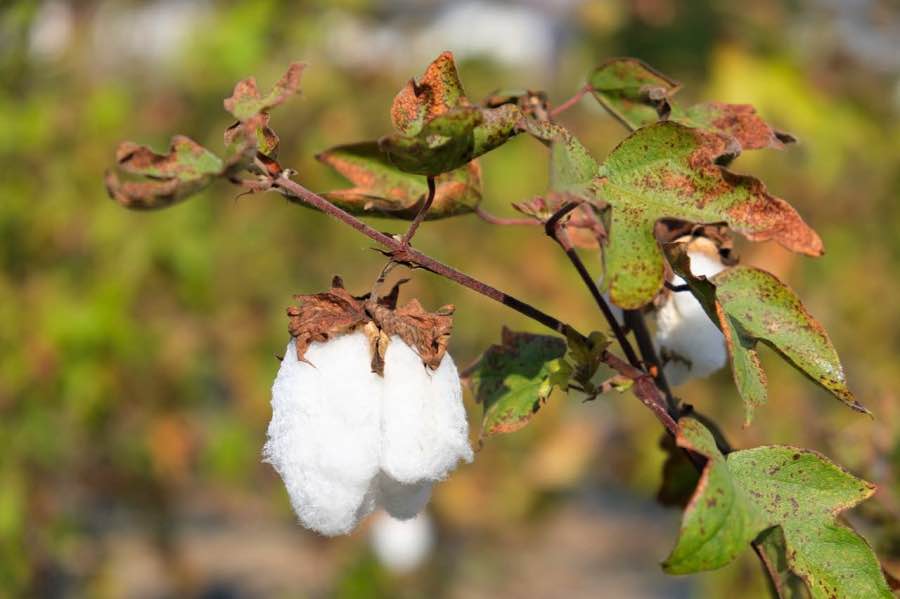
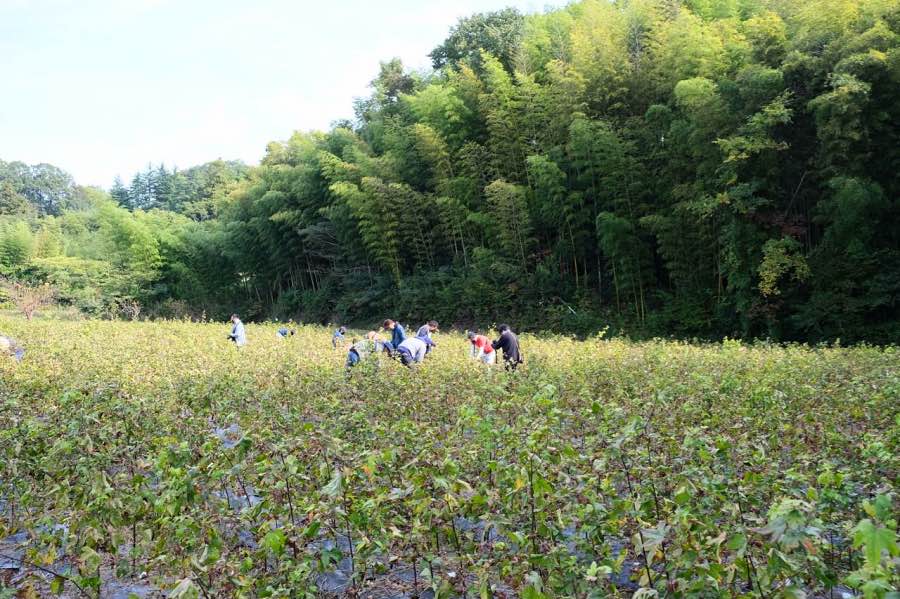
Harvest normally begins in October, and is again a team effort. The cotton is plucked carefully piece-by-piece, each volunteer using, you guessed it, a Samurai heavy denim cotton bag. This is usually done in stages, and can actually take until winter to complete as different fields hit their peak and the team works around the typhoons and heavy rains that hit the area each fall. For 2020, Samurai was able to harvest a total of 260 kilograms of raw cotton.
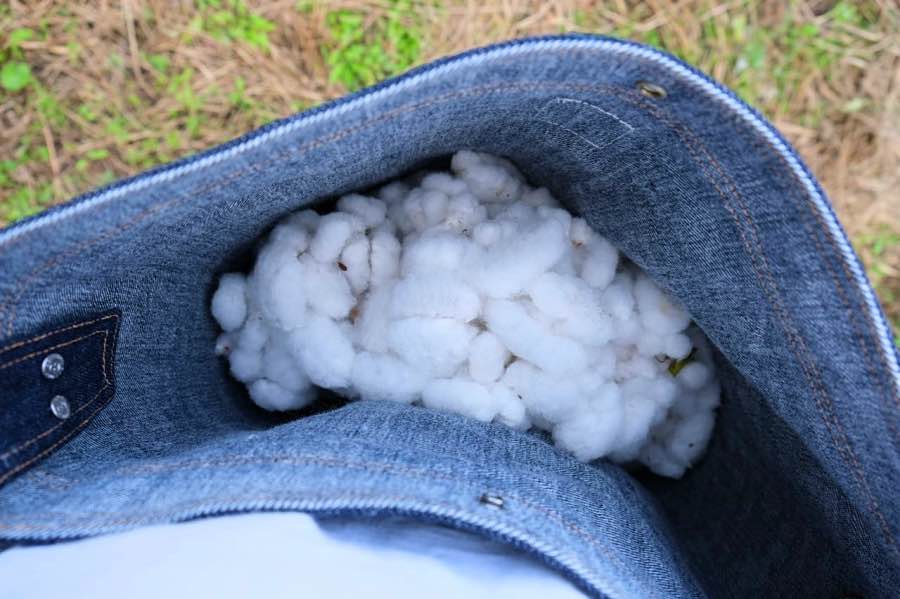
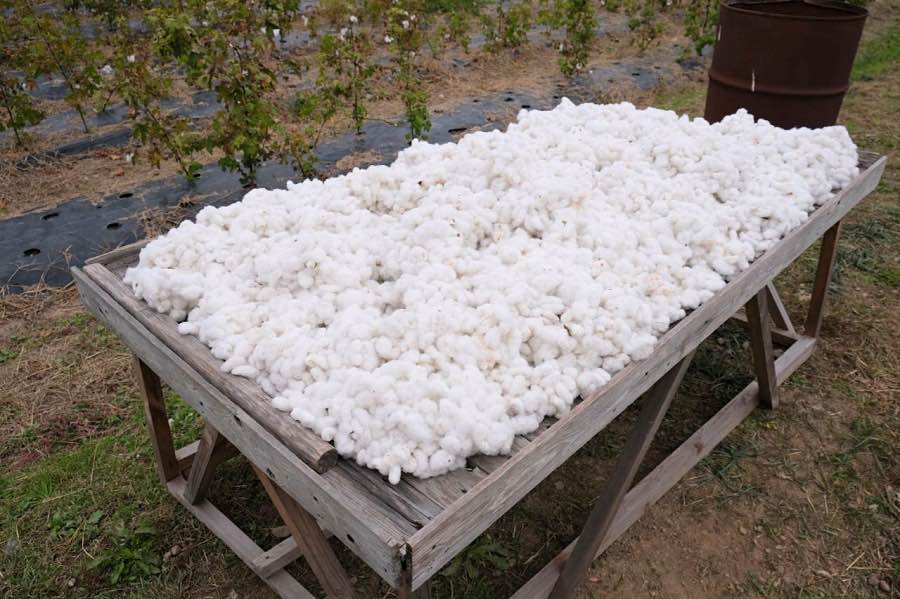
During the entire process, Samurai is also involving and giving back to the local community, and with local farmers, they have really resurrected cotton farming methods not seen in that area since the Edo period. They also host BBQs, sports festivals, and hold exhibitions at the local elementary schools where kids can learn about cotton, dyeing, etc.
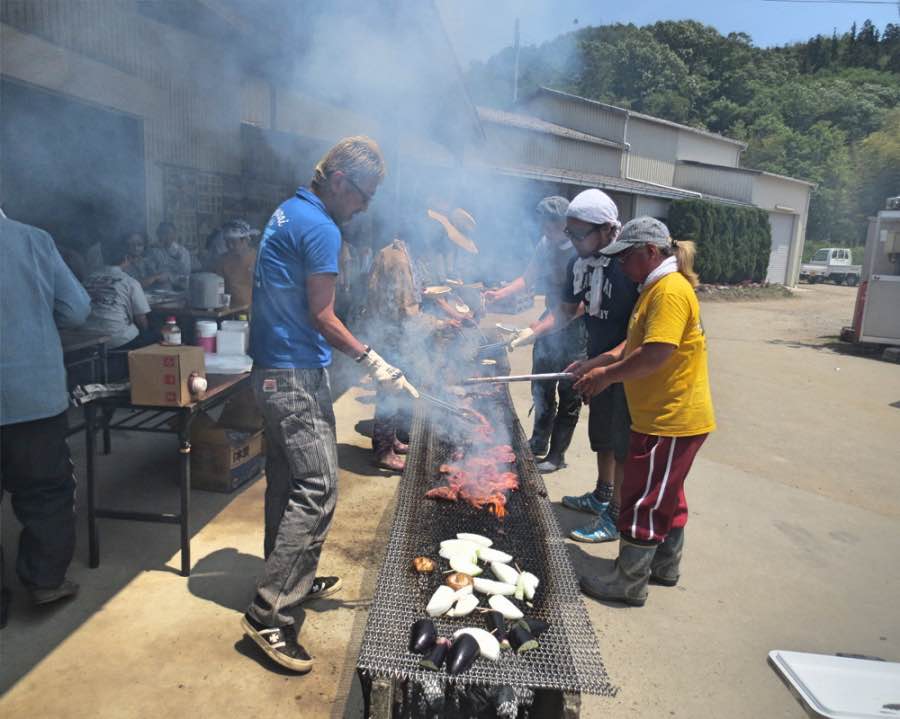
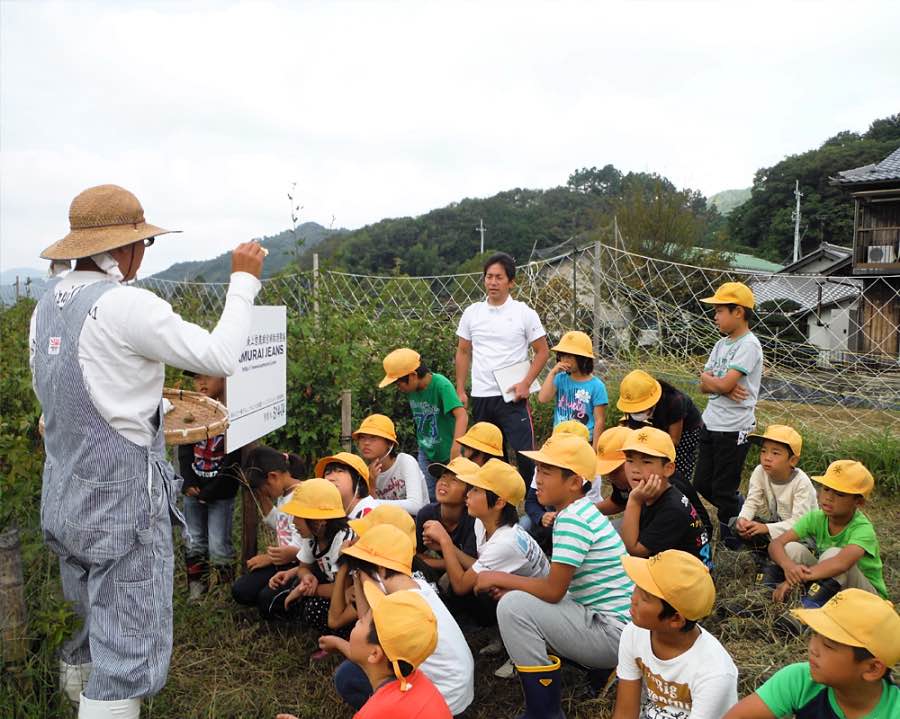
And for those fans who can’t actually make it out to the fields to help, Samurai gives them cotton seeds that they can grow at home. In the fall, Nogami-san collects their little Ziploc bags of fluff and it gets thrown into the mix. Every little bit counts.
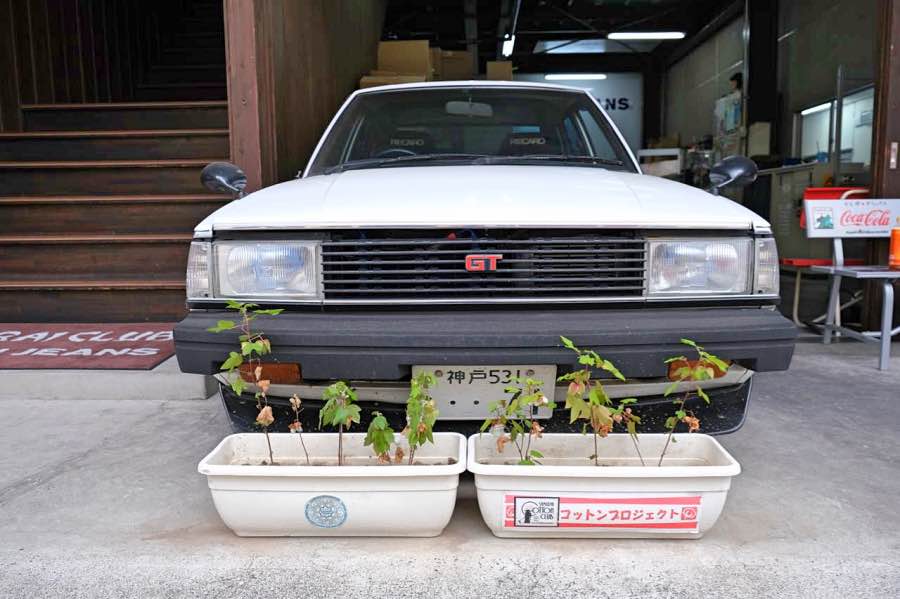
Once the cotton is harvested, it gets taken back to Samurai Jeans headquarters in Osaka where the seeds need to be separated from the fibers. When I asked Nogami-san how long this takes and he said, “About six months to a year”, I of course thought he was just being his usual funny self. Turns out he wasn’t. The staff work on it in their spare time, either by hand or using these little antique hand-cranked contraptions that bolt to the table. If you works hard, you can do about a kilogram a day with one of these wooden separators, meaning that 2020’s 260kg harvest could conceivably be done in 260 days of solid work. Now, of course Samurai could probably buy or borrow a modern machine to do this in a day, but that just wouldn’t be their style. This is old school, organic, every-step-by-hand kind of work. There is again that Japanese work ethic of liking things to be hard, making the fruits of your labor that much sweeter.
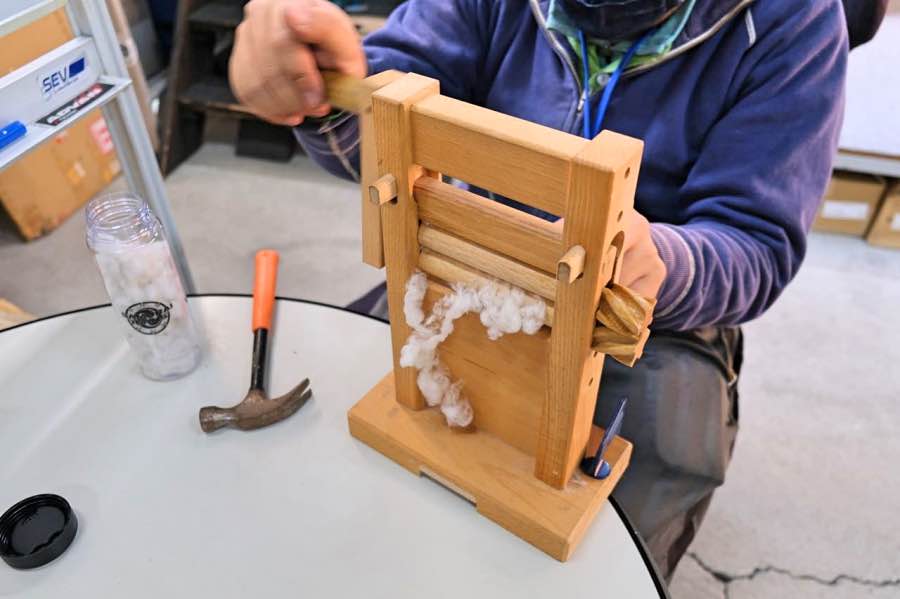
About the attributes of Japanese cotton itself, Nogami-san thinks for a moment and calls it “Kind….soft”, saying that denim made from their cotton has some unique qualities to it that you can see and feel. “But you know, we just don’t have enough cotton to realistically go on making jeans out of 100% Samurai cotton so….that’s why went with just using it for the weft.” At this point, because of the labor required and the low yields, Samurai is only using this cotton in a few of it’s jeans and a limited-edition jackets, though Nogami-san dreams of one day being able to use it in more of Samurai’s products. “I know that’s probably not a realistic aim in my lifetime, to use it in everything we produce, buy hey, one can dream.”
Though the price tag for the Cotton Project is still eye-watering by any appraisal (about $700 US here in Japan), I still don’t know how they manage to sell the jeans for as cheaply as they do, considering the sheer amount of time and year-round labor required. Though, in truth, I do know the answer: they lose money on each pair just to able to continuing doing what no other jeans company is doing.
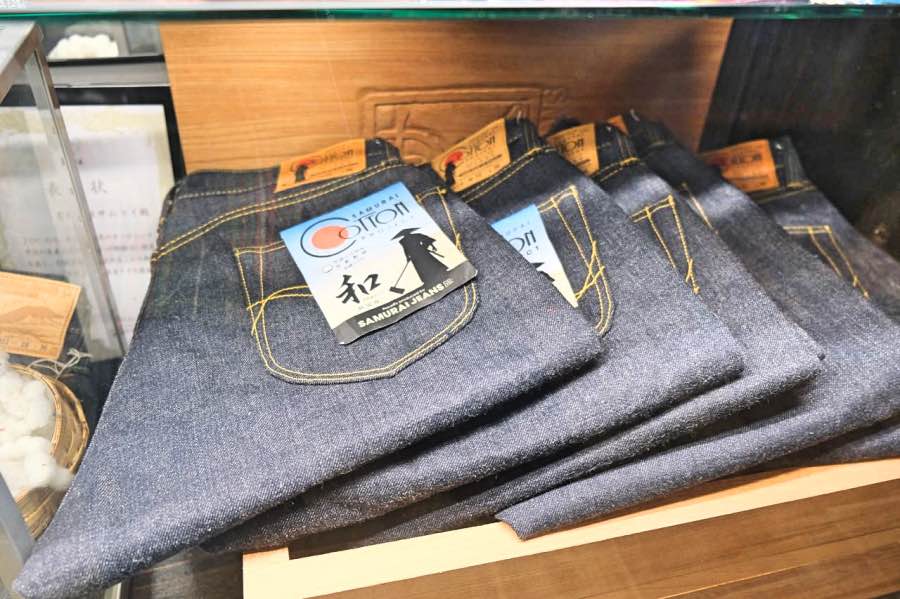
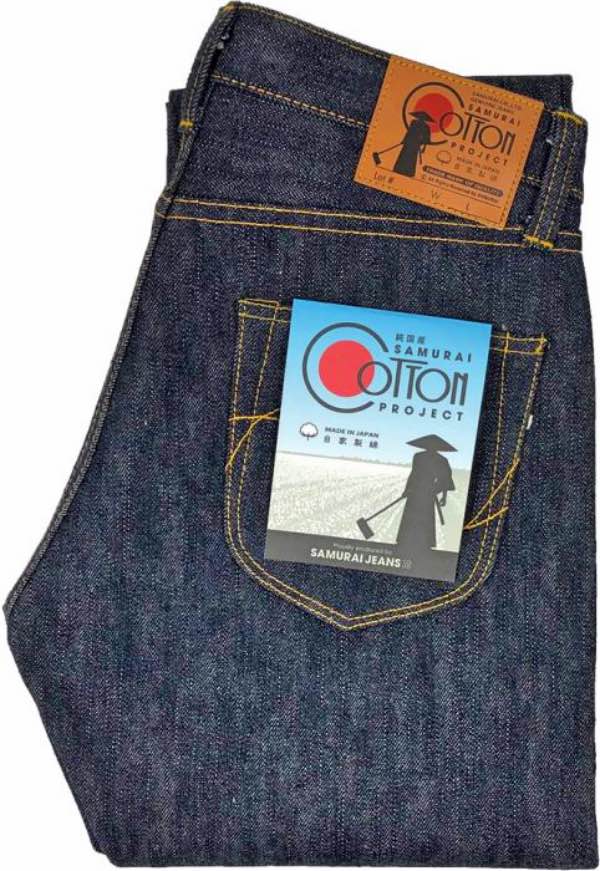
They also mix some of their Samurai cotton into the weft of their Ai+ jeans (about $350 US here in Japan) which is a bit of a cheaper way (relatively speaking) to own a bit of the magic. The Ai+ jeans also use natural indigo ,so you can kill two birds with one stone if “hon ai” (natural indigo) is another thing on your denim bucket list.
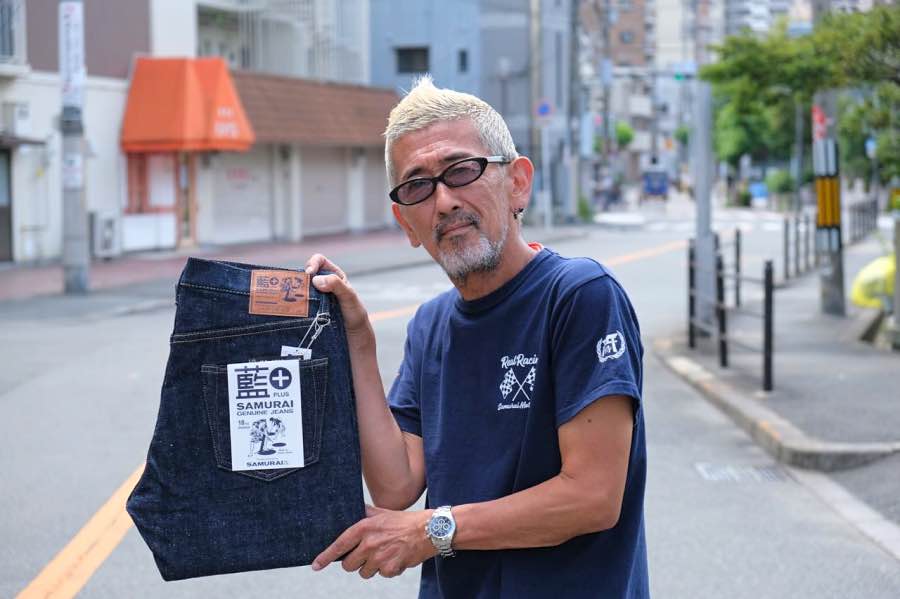
I feel honored to have been included in this amazing journey (having attended the planting and the harvest) and I have a real respect for what Nogami-san is trying to do. Couple Japan’s ageing and declining population with the serious issues of urbanization and loss of traditional and artisanal production of all types, and what Samurai is doing becomes a lot larger and more important than just trying to produce cool and rare jeans. Samurai is doing what no other jeans maker that I am aware of is doing and, in this particular case, they have revived a practice not seen since the age of….well, the samurai themselves.
Pingback: The Rise Of The Custom Denim Sneaker - The Weekly Rundown
Pingback: Self Edge Welcomes Samurai Denim To Its Roster
From south jersey reintroducing myself to your craft
The first ever pair of Samurai Jeans I happen to purchase was this pair https://redcastheritage.com/products/samurai-jeans-s710sc-ki-japanese-cotton-ecru-18oz-slim-straight-jeans which is part of the cotton project.
I have to say of all the brands and jeans that I own including other pairs of Samurai those are the most comfortable and so incredibly soft, textured and amazing…I can truly feel it and makes me love them all the more. I really appreciate the commitment to making 100% pure Japanese-made jeans and wish Samurai the very best in this journey and hope they continue to make more and more.
I look forward to a future pair
A thorough and wonderfully articulated story of the master of Samurai Denim Co and his struggle of love for his craft. Thank you for telling it.